Ford’s Iconic ‘Five-Oh’ V-8 Almost Born as Less-Sexy 5.8LFord’s Iconic ‘Five-Oh’ V-8 Almost Born as Less-Sexy 5.8L
“There's a lot of love and passion in the company and the customer base around the 5.0L engine,” Harrison says, “and we have wanted to do one for years.”
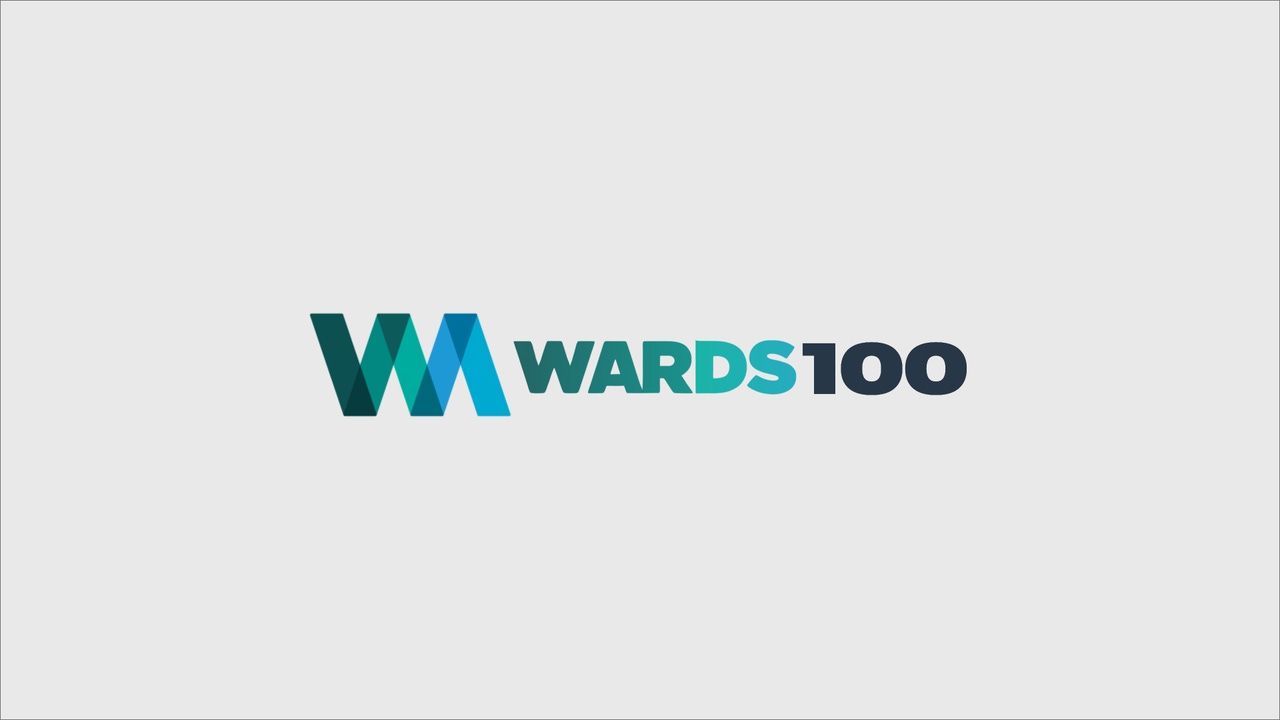
The Ward’s10 Best Engines competition has recognized outstanding powertrain development for 17 years. In this installment of the 2011 Behind the 10 Best Engines series, Ward’s looks at Ford’s new 5.0L V-8
One of the first things you notice about the ’11 Mustang powered by Ford’s new 5.0L V-8 is the big, bold “5.0” badge that adorns each of its sculpted front fenders.
bold 5.0 badges reflects passion of engineers, carries weight with enthusiasts.
Clearly, the folks at Ford are justifiably proud of the engine, especially those who worked on it.
“We had a lot of very passionate people working on the program, men and women who had Mustangs and wanted to be part of it because they felt emotion around it,” says Mike Harrison, Ford program manager-V-8 engines.
“There were a lot of people taking problems home on the weekends, working on them on their own time and bringing back solutions,” Harrison says.
Their new creation cranks out a very healthy 412 hp and 390 lb.-ft. (529 Nm) of torque from its 4,951-cc displacement. That is an impressive 83 hp/L compared with the 69 hp/L of the 319-hp 4.6L V-8 it replaces, and which was named one of Ward’s10-Best Engines four years in a row.
The new V-8 also offers decent fuel economy considering its prodigious output: 17/26 mpg (13.8-9 L/100 km) city/highway coupled to a 6-speed manual transmission and 18/25 (13-9.4 L/100 km) with the optional 6-speed automatic in the Mustang GT.
The new 5.0L shares no common parts with the outgoing 4.6L, though it does share the old “modular” V-8s’ bore spacing and its machining and assembly lines.
5.0L engine 100 lbs. lighter than proposed 5.8L.
Surprisingly, the new 5.0L V-8 almost was a 5.8L aluminum variant of the new 6.2L V-8 that powers Ford Super-Duty and Raptor trucks. That was the original plan.
“But there was a lot of consternation about having to re-engineer the mounts, exhaust system and other things underhood to fit that relatively large engine in there,” Harrison says. “And it would not have delivered the desired levels of performance or fuel efficiency.”
So the decision was made to design and develop a new aluminum-block 5.0L V-8 capable of 400-plus hp to compete with the 6.2L Chevy Camaro and the 6.1L Dodge Challenger Hemi V-8.
“There's a lot of love and passion in the company and the customer base around the 5.0L engine,” Harrison says, “and we have wanted to do one for years.”
But it would have to be done very quickly. “We eliminated a complete prototype phase and took 12 to 14 months out of our normal development cycle,” Harrison says. “Within a year of kicking off the program, we were running our first engine through mapping for calibration, which meant no more changes to cams, ports, exhausts or other things that affect calibration.”
And with 4-valve and Twin-independent Variable Cam Timing (Ti-VCT) technology, it could deliver high specific output with excellent fuel efficiency and would weigh only about 430 lbs. (195.5 kg), some 100 lbs. (45.5 kg) less than the proposed 5.8L.
Harrison adds that it was tempting to use the high-flow heads on the existing Mustang GT500.
But the team decided to completely re-engineer the heads and do new castings to achieve even better flow while at the same time make them more compact. This would enable a better-flowing intake manifold. Harrison credits his executive management for approving and supporting that plan.
“We had aggressive targets,” he says, “but great flexibility to execute what we needed and we weren't micromanaged. It's nice working in that environment. This is an iconic engine for the company, so we wanted to make it the best we could.”
Harrison lists the engineering team’s top priorities (in no particular order) as investment, performance, light weight, refinement and fuel efficiency. And by performance, he means “great peak power and a very tractable and flexible torque curve.”
FORD MOTOR CO.
Engine: | 5.0L DOHC 90˚ V-8 |
Displacement (cc): | 4,951 |
Block/Head material: | aluminum/ aluminum |
Bore x stroke (mm): | 92.2 x 92.7 |
Horsepower: | 412 @ 6,500 rpm |
Torque: | 390 lb.-ft (529 Nm) @ 4,250 rpm |
Specific output | 82 hp/L |
Compression ratio | 11.0:1 |
Assembly site | Windsor, ON, Canada |
Application tested | 2011 Mustang GT |
EPA city/ highway | 17/26 mpg (13.8-9 L/100 km) |
Pulse-separated exhaust manifolds give up to 15-lb. ft. (20 Nm) added torque at around 3,000 rpm, he says. “And the Ti-VCT enables us to vary exhaust cam timing independently from intake timing, which gives us very good low-speed torque.”
The engine essentially has two cam schedules: a fuel-economy schedule at part load (below half throttle) up to 3,000 rpm and a performance schedule for peak torque beyond half throttle.
“We have a lot of CFD (computational fluid dynamics) tools to manage airflow and design manifold runner lengths and cam schedules,” Harrison says. “We did over 32,000 cam-profile and timing-schedule iterations on the computer before settling on what we wanted, and we do both 1-D and 3-D fluid dynamics analyses. It’s kind of a virtual dynamometer.”
Among the team’s major challenges was achieving the power goal. “We were challenged by Derrick Kuzak, who said, ‘400 hp or we’re not gonna do the program,’” Harrison says.
“I had enough benchmark data to believe we could get there, but we could not be 100% confident. It took about six months to get confident and understand how to deliver it.”
Another challenge was assuring the durability of a 7,000-7,500 rpm V-8 engine. That meant understanding and managing the shaking forces and fatigue life of the components to ensure they would survive at such high-speed loads over extended periods of time.
The 5.0L’s Ti-VCT is a key competitive advantage, but the engine does not have direct fuel injection, partly because of DI’s added cost and complexity and also due to the short development time.
“The difficulty with DI is getting the fuel and air to mix well, because you squirt fuel into the chamber after the air is already there. Then you've got to mix it,” Harrison explains.
“It takes a lot of development work to execute it well, and it takes time to get that work done to get good mixing, and therefore, good fuel economy. If you don't do it well, you actually get significantly worse fuel economy than a well-executed PFI (port fuel injection) engine.
“We were challenged for a time because the Camaro and Challenger were coming on strong, so we leveraged known technologies such as PFI to execute it well.
DI systems still are expensive and it is difficult to make a business case to implement the technology without combining it with turbocharging, Harrison says.
However, he adds the 5.0L architecture is designed to accommodate DI. Engine prototypes using DI were built and tested, so the technology could be added when it makes sense. Is there room for future improvement beyond that?
The team is working on improving efficiency through friction reduction, improved cam timing and other measures “for incremental tenths of percent in improvements,” Harrison says.
“Some think we can change the laws of physics and achieve 10% to 15% (fuel-economy improvements). But the next 2% or 3% will come in conjunction with improvements in aero drag and friction on the vehicle. It's going to be a very slight evolution.”
Read more about:
2017 10 Best EnginesAbout the Author
You May Also Like