Steel Turns Green
This month, workers at the Curtis Screw Co. in Buffalo, NY, will begin machining a part for Ford Motor Co. using a new unleaded "green steel." Bob Squier, president of Curtis, calls it a significant development for the industry because the new steel helps bring a truly environmentally friendly car closer to reality.Curtis is one of the largest screw machine parts suppliers to Detroit and a member
August 1, 1999
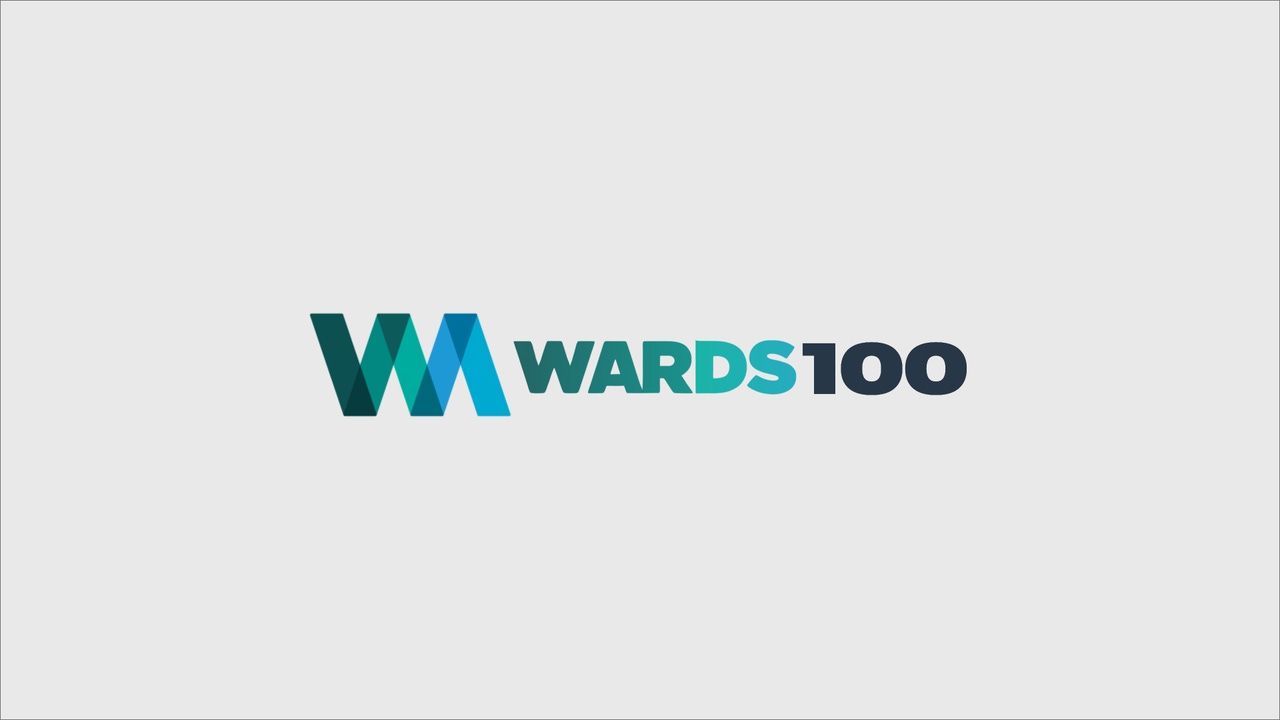
This month, workers at the Curtis Screw Co. in Buffalo, NY, will begin machining a part for Ford Motor Co. using a new unleaded "green steel." Bob Squier, president of Curtis, calls it a significant development for the industry because the new steel helps bring a truly environmentally friendly car closer to reality.
Curtis is one of the largest screw machine parts suppliers to Detroit and a member of the Nonleaded Free Machining Steel Consortium LLC. The NFMSC financed a four-year development project at the University of Pittsburgh's School of Engineering, where green steel was created. Professors Anthony J. DeArdo and C. Isaac Garcia headed the development team.
Pitt has filed for a patent that's expected to be issued this month. The new lead-free machining steel is intended as a substitute for 12L14. That leaded steel alloy is widely used for manufacturing fuel injectors, flywheels, brake and air conditioning components and numerous other parts for trucks and cars. What these and all screw machined parts have in common is that they are made in high volumes and their specifications call for very close tolerances.
Production volumes for these parts range from 3,000 up to 100,000 units per day, Mr. Squier says. Many of the parts have more than 75 dimensions. In tests, the parts can be more easily machined from green steel than 12L14. "That may enable us to drop the prices of parts we sell to car manufacturers, and that will certainly get their attention," Mr. Squier says.
Another factor is environmental. A tremendous amount is spent on pollution-abatement equipment. "We can eliminate all that," Mr. Squier says.
The new unleaded steel also will make recycling easier. "You can't just melt down leaded steel and reuse it," Mr. Squier says. He notes that Curtis must pay someone to cart away the tiny scrap chips that now are created when machining parts out of 12L14. The green steel chips could be recycled easily without any special handling.
The market for 12L14 steel ranges between 2 million to 3 million tons per year. Approximate cost is $500 per ton. That makes the business for green steel a potential $1 billion-plus market.
Producer members of the consortium who have the right to produce green steel, besides Curtis, include United Alloys & Steel Corp. also of Buffalo, MacSteel, Ft. Smith, AR; Saarstahl AG, Volkingen, Germany; and Laurel Steel, Ont., Canada. USS/KOBE Steel Co. has also supported the research and has the option of joining the consortium.
Ispat Inland Steel Bar Co. did not participate in the consortium, but Jeffrey Webb, manager of sales and marketing, says Ispat Inland has sold a free machining steel called "Incut" for 20 years that contains no lead. The steel is patented, and uses bismuth to obtain the desirable free-machining characteristics. Mr. Webb says Incut is competitively priced as well.
Milton Harris, chairman of Harris Steel, the owner of Laurel Steel, says major automakers in the U.S. and Germany have indicated their desire to use green steel if it is economically competitive.
The researchers say that the key to developing their version of green steel was in asking the right question, attempting to understand what lead does in 12L14 steel on an atomic level.
They used an atom probe field ion microscope to examine leaded steel. Mr. Garcia says the microscope is capable of magnifications in the millions - to the point where individual atoms can be seen. Then the team peeled back atom by atom to discover precisely what lead did in 12L14.
Mr. DeArdo says "once we saw what the lead did, the answer was obvious to us."
The two professors decided that tin would be the most suitable substitute for lead. Then it took a lot of experimentation to determine the best ratio of tin to steel. Too much tin made the steel brittle and harder to machine. The optimum tin content, they discovered, requires adding far less tin than lead. Thus, the actual cost of green steel may not be higher than 12L14.
Curtis Screw is in the process of running trials for both GM and Ford. DaimlerChrysler is not a direct customer, but Mr. Squier says that Curtis makes parts for DC's major suppliers.
About the Author
You May Also Like