The QUALITY CRUNCH
If you only read the headlines, it doesn't look like Ford Motor Co. can do much right these days. Besides its high-visibility fight with Bridgestone/Firestone Inc. over tire recalls and sport/utility vehicle (SUV) rollovers, it seems like the company has forgotten how to build quality cars and trucks. Ford's problems already have been well documented: Its Escape small SUV has been recalled five times
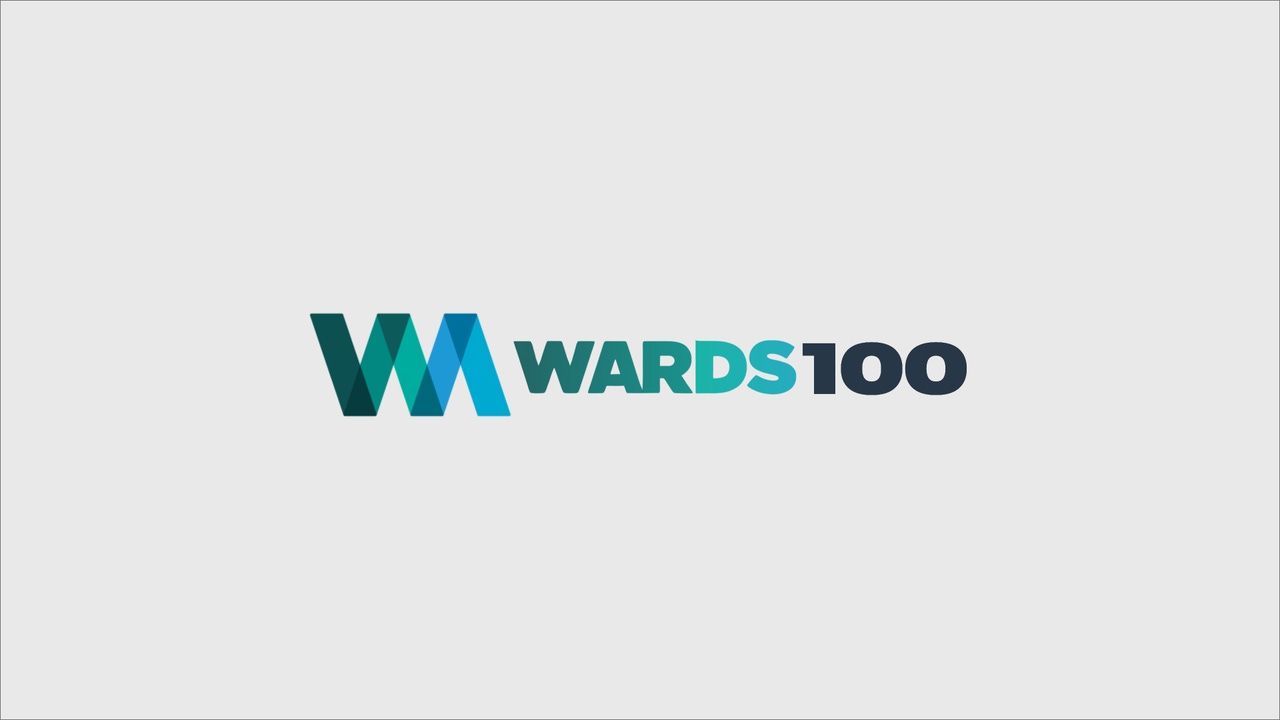
If you only read the headlines, it doesn't look like Ford Motor Co. can do much right these days. Besides its high-visibility fight with Bridgestone/Firestone Inc. over tire recalls and sport/utility vehicle (SUV) rollovers, it seems like the company has forgotten how to build quality cars and trucks.
Ford's problems already have been well documented: Its Escape small SUV has been recalled five times in the past year. The crucial launch of the Ford Explorer — an excruciatingly slow event that was meant to eliminate glitches — already has been marred by two embarrassing recalls.
The last recall, which involved 50,000 Explorers built at the automaker's Louisville, KY, plant — appears particularly bone-headed: Tires on some trucks were cut by a sharp edge on a narrow stretch of the assembly line because nobody told the factory the new Explorer's stance was a little wider than the old one.
Before that, the launch of Ford's Focus subcompact was plagued with numerous recalls. And, to top it all off, Ford trailed General Motors Corp. and DaimlerChrysler Corp. — as well as Toyota Motor Corp., Honda Motor Co. Ltd., Nissan Motor Co. Ltd. and Volkswagen AG — in the most recent J.D. Power & Associates survey of initial vehicle quality.
Recalls set a record pace
Even so, most competitors have little room to gloat.
Recall rates have soared over the past several years for almost all makes. Even quality leaders such as Acura and Mercedes-Benz are calling back vehicles to fix glitches. And in some cases these problems are every bit as scary and embarrassing as Ford's.
Earlier this year, GM recalled 6,000 ’02 Chevy TrailBlazer/GMC Envoy/Oldsmobile Bravada SUVs because of a faulty suspension part. It was serious enough that GM asked owners to stop driving the trucks immediately because failure of the lower control arm on the front suspension could cause the driver to lose control. Dealers towed the vehicles and provided loaners pending a fix.
GM ordered more than 50 different recalls in 2000, compared with 35 in 1999, according to initial government figures obtained by WAW. That's less than Ford's 61 recalls last year, but not exactly a low number.
Likewise DaimlerChrysler ordered about 30 recalls last year compared with 28 the year before. DC also has been in the headlines recently for several safety-related recalls. In early June it announced it was recalling 136,500 of its ’01 Chrysler and Dodge minivans for “product improvement” because the left side sliding door opened in government crash tests.
All this publicity, coupled with product liability lawyers trying to sway public opinion in their favor and a smattering of anecdotal evidence from friends and co-workers who have had problems with brand new cars, has many consumers wondering if a quality crisis is brewing.
So far, however, most analysts attribute the growing recalls — many of which are related to very minor problems — to vehicles that are becoming more complex every year and a much more cautious attitude by automakers fearful of litigation. The more serious problems are blamed on high-volume operations, supply chain screwups and trying to move too fast with new technology and new designs.
Yet by just about any measure, a new vehicle bought today has far fewer problems than it had 5 or 10 years ago. Many are being recalled for items that engineers didn't even think were a problem in the 1970s.
And some consumers see recalls in a positive vein, as a sign automakers want to update and improve their products even after they've left the showrooms.
But there are limits. Consumers are a lot more knowledgeable and discriminating than they used to be, and a lot less forgiving.
“Whether it's a perception or real problem is immaterial,” says California car dealer Kent Hagan. “Perception is reality in a consumer's market.”
Quality miscues are so pervasive they've reshaped our culture by infusing our vocabulary with new words.
Two decades ago, “delamination” was heard only in body shops. Today, thanks to a notorious industry experiment that eliminated a primer coat during the painting process and later caused paint to peel off nearly new cars in big sheets, the term nets thousands of hits on the World Wide Web.
Meanwhile, some old expressions are given new significance. Say “side-saddle” and you are more likely to envision GM fullsize C/K pickups bursting into flames than Dale Evans riding off into the sunset with Roy Rogers.
Just how did this all happen? Consider:
National Highway Traffic Safety Admin. records show more than 250 vehicle recalls as of mid-June — well on pace to exceed last year's record 12-month total of 483. The 2000 total broke the previous high of 370 — set in 1999 — and shattered the next-highest mark of 328, set the year before.
Numbers of recalled vehicles have risen correspondingly — 23.4 million in 2000, 19.2 million the previous year and 17.2 million in 1998.
Vehicles snared by non-compliance recalls — issued for failure to meet the Federal Motor Vehicle Safety Standards — increased to 4.5 million in 2000. This represents a 61% hike compared to 1999's 2.8 million, and it's nearly three times the 1.6 million recorded in 1998.
A total of 18.9 million vehicles were recalled in 2000 because of safety-related defects, NHTSA tells WAW. That's 81% of the overall recall total and a sharp increase compared to 1999 and 1998, when safety-related defects prompted recalls of 16.4 million and 15.6 million, respectively. Even more telling, perhaps, it's 9% more than the 17.3 million new light vehicles sold last year in the U.S.
So great was NHTSA's workload last year that the agency was forced to hire additional staff. Yet its annual report on safety-related recall campaigns — usually published in July — is not expected until next month.
Meanwhile, industry insiders and observers maintain automotive quality isn't on a major downhill slide.
The blame game
But somebody always seems to be asleep at the switch. The most popular culprits — or scapegoats — are suppliers.
Unofficially, it's been open season on them since April 23 when the Sales & Marketing Executives of Detroit named Ford group vice president Richard Parry-Jones, “marketing statesman of the year.”
With an uncharacteristically harsh tone, he used the podium to plant a seed with suppliers.
“My message to suppliers is this: Work with us on improving quality — cost and profits will correct themselves,” Mr. Parry-Jones tells the crowd. “I will do anything I can to help you out on quality.” The comments came from out of the blue. But they didn't rankle. Perhaps because suppliers have been feeling the heat for some time.
Share of the Blame
Total vehicles recalled (US) | Share of total vehicles recalled | Share of total vehicles sold | ||||
---|---|---|---|---|---|---|
1999 | 2000* | 1999 | 2000 | 1999 | 2000 | |
DCC | 5,719,804 | 6,590,052 | 29.7 | 28.2 | 15.6 | 14.5 |
Ford | 6,398,883 | 7,485,466 | 33.3 | 32.1 | 24.5 | 23.9 |
GM | 3,557,662 | 5,806,857 | 18.8 | 13.6 | 29.4 | 28.3 |
Toyota | 589,190 | 8,379 | 3.1 | .03 | 8.7 | 9.3 |
VW | 277,571 | 191,418 | 1.5 | 0.9 | 2.2 | 2.8 |
Source: National Highway Traffic Safety Admin. and Wards Automotive Reports. |
Stricken last year by 61 recalls that had the potential to affect 7.5 million vehicles, Ford not only is reviewing and revising its own practices, it is actively urging its suppliers to do the same. Even to the point of enrolling them in Ford's own quality improvement program: “consumer-driven Six-Sigma.”
Says Bo Andersson, GM's executive in charge of worldwide purchasing, regarding the new midsize SUV launch: “The responsibility given to suppliers has changed dramatically. … We have 500 to 600 suppliers having 3,000 new part numbers. We have more Tier 1s, Tier 2s and Tier 3s that are playing a much bigger role than they used to in the past. A lot of that stuff used to be done by General Motors, developed by General Motors.”
A supplier executive, who wants to remain anonymous, bristles at the suggestion that quality problems fall at the feet of suppliers. He says quality has suffered because of the Big Three's relentless pursuit of cost reduction. He also suggests that buyers at the Big Three are evaluated more based on cost saving than on the quality of parts they procure.
Both Mr. Andersson and his counterpart at DCC, Thomas Sidlik, executive vice-president of procurement and supply, adamantly deny this claim.
“I can show you my monthly report that I send into my boss, and what's on there is technology, cost, delivery and minority sourcing,” Mr. Sidlik says. He uses a similar process to evaluate the Chrysler Group's suppliers. “So everyone is responsible. Quality is No. 1 on my sheet.”
Mr. Andersson agrees, and he does not see a correlation between GM's aggressive campaign to drive down costs and its attempts to reduce defects.
“Today if you ask our suppliers, they say in certain areas our three priorities are quality, quality, quality. In certain areas, our priorities may be cost, cost, cost. If you take glass and steel, quality is not a big issue. If you take generators, our priority is quality because when you look at our warranty costs, it kills us.
“When we come down to the root cause today, in the supplier area it's very much Tier 2- or Tier 3-related problems,” Mr. Andersson says, adding that Tier 1 suppliers need to work more aggressively with these lower tier suppliers on manufacturing efficiency and on the QS-9000 quality system.
But the general manager of a small company that works with automakers and Tier 1 and Tier 2 suppliers, says OEMs and top tier suppliers should look in a mirror when looking for someone to lecture about quality.
At DCC, there is continuity, he says. The liaison person is usually the same throughout the life of a project. But at Ford, he says he'd start dealing with one person for a few weeks or months and then he or she would be reassigned.
“No one ever wanted to sign off or take responsibility for anything,” he says, claiming some jobs are approved even though specifications are not met.
GM is better, the supplier says. While its bureaucracy is daunting, communication is superior once you find the right contact person.
He also says big Tier 1 suppliers often do a poor job of managing their businesses. And while many have beautiful headquarters buildings, their factories can be second-rate, filled with old equipment and poorly trained workers.
Holding suppliers responsible for warranty costs has been a hot button since GM and Ford raised the issue four years ago. GM calls its program “risk and reward,” which holds a supplier responsible for a product's design.
“If that supplier is exceeding the warranty commitment, we pay that supplier money. They get a bonus check on a yearly basis,” Mr. Andersson says. “If the supplier is missing his warranty target, then he needs to pay a portion of that warranty.” While suppliers in general are improving, he says GM receives three checks from partsmakers for every one it sends to a warranty-free supplier.
There is some consensus outside the industry to support a blame-the-supplier position in some instances. Of the recent GM SUV recall caused by a potentially defective suspension part, David E. Cole, director of the Center for Automotive Research (CAR) at the Environmental Research Institute of Michigan (ERIM) is succinct:
“The supplier just blew it,” he says. “What they designed and tested isn't what they built. It could have been a simple little thing, a little change in the heat treatment process. Suddenly, it became a big deal.”
Rosemary Shahan recognizes this behavior pattern. The founder of Consumers for Auto Reliability and Safety (CARS) says obstinacy, even in the face of impending disaster, is rooted in the industry's culture. It was there in the 1970s when Ford decided to leave the Pinto unchanged despite evidence its gas tank needed a shield to protect it from puncture. And, she claims, it continues today — ironically citing Ford for its position on an ignition module allegedly prone to malfunction because its placement in the engine compartment causes overheating.
Despite Ford's data-backed assertion that the modules perform as well as their competitors' modules, a California judge wants the automaker to recall 1.7 million suspect vehicles.
Industry gadfly Clarence Ditlow of the Center for Automotive Safety suggests automakers would eat their own kind before changing course on a product. Even when suggestions come from within, he says, they've been ignored.
“I was truly amazed with GM's 1980-to-1988 front-wheel drive power steering system with rack-and-pinion,” Mr. Ditlow recalls. “Engineers wanted to go back to cast iron from aluminum. They were just wearing it out. And they had any number of recommendations from the engineers to change it. But it took them eight years to change it.”
Ms. Shahan sees signs of hope. “I have to give Ford some points for doing this more expansive recall now of their tires,” she says, referring to the recent decision to replace 13 million Firestone tires on Ford vehicles, primarily the Explorer.
The best defense …
Independent analysts like CAR's Mr. Cole and Jim Matyeka of A.T. Kearney say automaker determination to detect and eliminate potential defects as quickly as possible — before they turn into litigation nightmares — is a big reason why recall rates are rising.
“They're doing some things now they never would have done years ago. There's a higher sensitivity to want to prevent bad things from happening,” says Mr. Cole.
“At GM we look at recalls in a negative light because it means we made a mistake,” says Bob Lange, GM executive director of safety integration. “From a consumer standpoint, I'd like to think we could make a recall and not have customers dissatisfied. I hope it results in some positive experiences too, not just negative.”
That's how it is in Europe, says Louise Goeser, Ford's vice president-quality. “European customers have a different view of recalls,” she says. “They look at a manufacturer stepping up to an issue and recalling and taking the action to bring vehicles in, getting them fixed, taking care of it, as being very responsible. … And that's the way I like to think about it. We don't want to make mistakes, but if we find an issue — even if we think it's very low probability that it will ever happen — we want to take care of it.”
But why not plan better, thereby avoiding problems? That's everyone's goal, but, says Lexus vice president and general manager Dennis E. Clements: We deliver.
“I don't know that you can judge quality based upon recall,” says Mr. Clements, who knows whereof he speaks because Lexus shines in this year's J.D. Power & Associates 2001 Initial Quality Study (IQS), claiming top honors in three out of the four segments in which it has entries.
Not surprisingly, Mr. Clements favors the renowned study over recall totals as the best yardstick to measure quality — but not just because Lexus fares well.
“If you look at the J.D. Power numbers, they suggest that everybody's quality's improving,” he says.
Indeed, J.D. Power's IQS — which surveys new vehicle buyers about their first 90 days of ownership — shows the gap closing between Asian automakers, the perennial quality champs, and their European counterparts.
In 2000, the study says, automakers based in Asia recorded 140 problems per 100 vehicles (pp100) — two fewer than last year. Meanwhile, European brands trail by one with 141 pp100 after recording 154 pp100 last year. American automakers bring up the rear with 153 pp100, an improvement over last year's total of 164 pp100.
So why the negativity? “It may just be a few very visible quality issues (such as Ford's tire troubles and recall numbers) are spotlighting the issue for the industry,” says Mr. Cole.
“I don't see a sense that quality is disintegrating on the vehicles at all,” he says, noting last year's record sales year is rife with mitigating circumstances.
High tech can add glitches
Mr. Cole attributes many recalls and quality problems to the high degree of technological sophistication being integrated in today's vehicle designs. Similar problems occurred in the 1980s when automakers were struggling with tight time frames in a bid to meet tough new emissions standards. This climate forced electronic systems into production before they were ready.
Mr. Mateyka concurs. “Complexity is a packaging issue. The engine compartment gets very, very stuffed,” he says.
A typical recall nowadays: Mr. Cole says his GMC Jimmy (SUV) is being recalled. The software algorithm on the ABS system needs to be changed. If the vehicle comes off a slippery surface such as ice, the software doesn't adjust the antilock braking system quickly enough so it can adapt to a different surface. It basically needs to be reprogrammed. Since Mr. Cole doesn't plan on encountering any ice until next winter, he's not concerned about the problem.
“If you look at defect recall patterns, there is usually an assembly interface overlap, something rubs something else that it shouldn't. Those are very difficult-to-eliminate problems,” says Mr. Mateyka.
In addition, American automakers “tend to be more aggressive with designs, things that might compromise,” Mr. Cole adds.
“We tend to take big jumps. Honda and Toyota are more conservative.”
While he hints Lexus has designs on its drawing board that will change its staid image, Mr. Clements challenges the claim that manufacturing problems are so thorny, they can excuse error.
“It's all process,” he says, noting Toyota annually churns out 500,000 Camrys, Avalons and Siennas at its Georgetown, KY, plant — and it gets a 101 pp100 rating from J.D. Power.
In this process, known formally as the Toyota Production System, every worker is not only empowered, but roundly encouraged, to slow or even stop the line if problems arise.
“And that happens hundreds of times a day,” says Barbara McDaniel, spokeswoman for Toyota Motor Mfg. North America.
Says CAR's Mr. Cole: “In door part quality, Americans conform best to specification. Yet, when it comes to J.D. Power … the guys with the worst part performance (Japanese automakers) have the best system performance.
“It's called ‘functional build,’” he adds. “We build to print and specification. Japanese build to function.”
Many European automakers also enjoy solid quality reputations, but Mr. Cole calls their approach “brute force quality,” which requires repeated inspections and rework before the finished vehicle leaves the factory.
Mr. Sidlik, of DC, has heard all this before. And he admits to being “tired of the negative attitude around Detroit that, well, the imports are better.”
The data doesn't support such perceptions, he says.
“Take a look at J.D. Power — (Chrysler) Concorde is No. 1 in its class!” Mr. Sidlik exclaims. “See how great Jeep did? We tied Toyota, didn't we? Grand Cherokee tied with Toyota in its class.”
He says he's proud that Consumer Reports recommends 74% of Chrysler Group's vehicles. “They haven't been easy on us when our quality hasn't been where we want it. Now they recognize the great quality we have. Take a look at some of the reports — we're one of the few manufacturers that had over 50% of their vehicles rate above the segment average.”
So, is the public perception off base? Is quality improving industry-wide?
“It's happening,” says Ms. Shahan. “I started out on lemon issues back in ’79, and when you look at the cars that were produced then, they were falling apart on the road. You had the Plymouth Volare (one of the most awful cars of an awful decade). Need I say more?”
Automakers are beleaguered, she adds, “because people's expectations have gone up.”
Mr. Mateyka agrees, saying details that would have been ignored 25 years ago get considerable attention today. “Long-term failures of metal parts, if you went back to the '70s, you'd see zero recalls of that type. It's clear the standards have gone way, way up.”
Technology, which currently is part of the problem, also promises to be part of the solution. New, more comprehensive diagnositic systems should be able to eliminate many problems, predict others and make recalls easier and faster. Electronics such as tire pressure sensors will help drivers avoid maintenance problems that could turn into crashes.
Most importantly, they will help drivers gain back the trust in their vehicles that some consumers are losing. “Trust is more important than quality,” Mr. Cole asserts. “That's why Ford is going to such extremes. To consumers, trust means buying a safe product for your family. We're always going to find differentiators in terms of quality. The trust issue is just a real killer one in the middle of this.”
About the Authors
You May Also Like