10-Day Launch?Admittedly, Honda's fast, but maybe not that fast
SAYAMA, Japan - The Japanese word for it is tachiagari. Elsewhere in the world it's known as "ramp-up" - the process of raising production volume of a new model to target levels.And Honda Motor Co. Ltd. is one of the fastest.The automaker's record in the United States has been widely reported - only 20 days to launch the Accord in August 1997. Not widely reported, Honda took only 10 days to launch
March 1, 1999
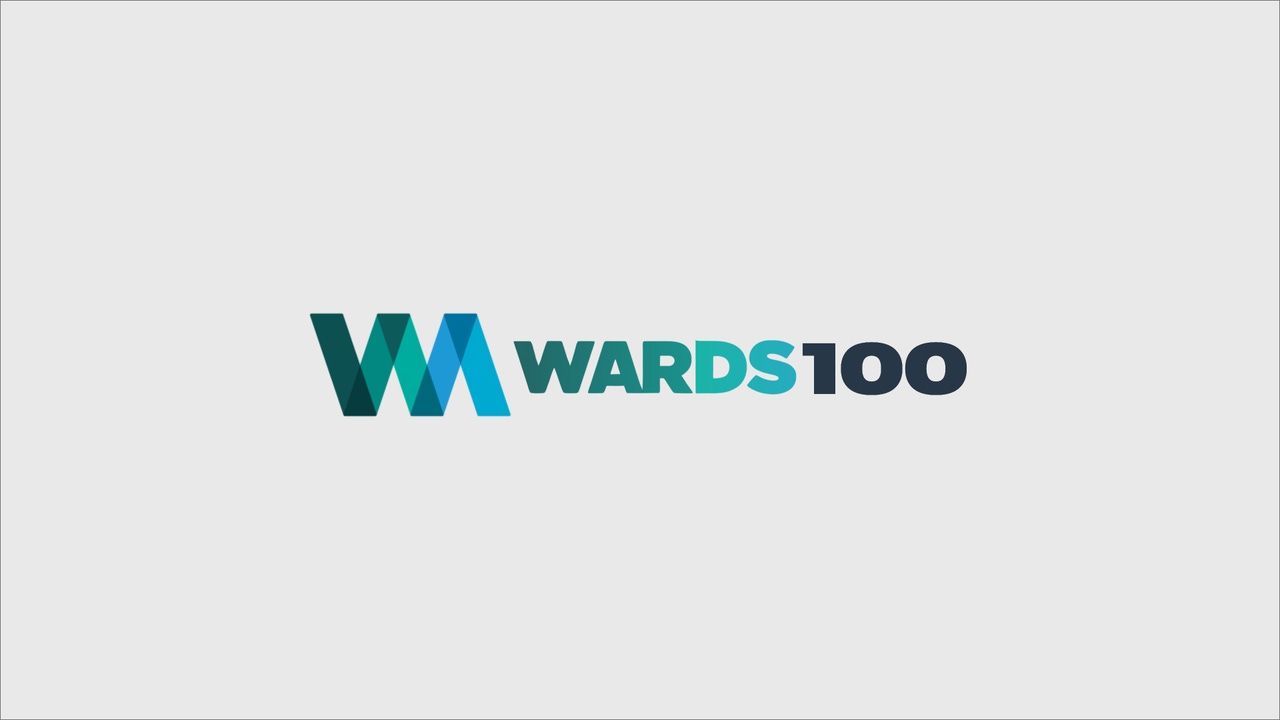
SAYAMA, Japan - The Japanese word for it is tachiagari. Elsewhere in the world it's known as "ramp-up" - the process of raising production volume of a new model to target levels.
And Honda Motor Co. Ltd. is one of the fastest.
The automaker's record in the United States has been widely reported - only 20 days to launch the Accord in August 1997. Not widely reported, Honda took only 10 days to launch the popular model in Japan one month earlier, arguably the fastest ramp-up of any bread-and-butter model in the world.
Many outsiders consider such speed impossible. Even within Honda, comparisons between the company's U.S. and Japanese operations are often misleading. For example, Honda of America Mfg., which builds the Accord in Marysville, OH, designates "Job One" as the first model to roll off the line on the day production of the old model ceases and is replaced by the new. The fact that hundreds of trial production units, built weeks and months ahead of the official startup, were sold through Honda dealerships is inconsequential.
Contributing to the confusion, the U.S. and Japanese Accords are two distinct models. Though sharing the same "flexible" platform, the American model is 4.3 ins. (11 cm) longer, 3.5 ins. (9 cm) wider and 0.6 ins. (1.5 cm) shorter, and there are few shared components between the two cars.
In addition, the Marys-ville plant is 18 years newer than Honda's aging auto plant located here, home of the Japanese Accord. More importantly, the Ohio facility is blessed with all the advantages of space - some 3.1 million sq. ft. (288,000 sq. m) under roof on a single floor with ample distance between lines and even more room for expansion - all unavailable to Honda when Japan's youngest automaker opened the two-story Sayama plant in 1964.
Finally, ramp-up objectives are different. That's not surprising, considering that the domestic Accord must share its Sayama production line with five other models (three excluding the Accord wagon and Torneo sedan, both derivatives).
Honda of America, Honda's main overseas production unit, builds Accord sedans on both Marysville lines and on each a smaller volume derivative - the Acura CL on Line One and the Accord coupe on Line Two.
At Sayama, the Japanese Accord is built on Line Two of the plant along with the Torneo sedan, Acccord wagon, Odyssey minivan, Legend sedan and - since July of last year - the longer, wider U.S. Accord for export to North America; Honda added the model to meet a capacity shortage at Marysville.
The CR-V, Odyssey and Prelude occupy Line One.
This mixture of models and resulting increased complexity make comparisons even more problematic. At Marysville, for instance, combined "model-type-color" variations for both Accord lines slightly exceed 1,100, whereas at Sayama, for the Accord sedan only, there are 1,650 variations.
Including other models built on the line, the total approaches 8,200.
Counting Line One, where the CR-V is the main product, variations exceed 11,000.
Moreover, four of the models on Line Two have essentially different platforms of varying lengths, widths, wheel bases and engine types. Only three (the Accord and Torneo sedans and the Accord wagon) share major components such as seats, steering wheels and instrument panels.
Complexity only tells a part of the story, however. The Accord launch in Ohio set out to build 1,750 units in 20 days, raising output by nearly 30% in the process. Sayama's objectives were far more modest: 130 units in half of the plant.
"The biggest difference between our system and theirs (Honda of America Mfg.) is that we produce a broader mix of models on our main assembly lines," says Honda executive Motoatsu Shiraishi who adds: "Thus even if we want, we can't afford to disrupt production to introduce a new model."
While the Accord ramp-up took place at Sayama in July 1997, Honda continued to produce the Odyssey, Legend and Inspire (no longer made in Japan) on the line. Combined output in the period immediately preceding the launch averaged 12,100 units per month, slightly over half capacity, as customers withheld purchases until the new model went on sale.
Meanwhile, Sayama's Line One sped along at more than 100% utilization, with output for all of 1997 exceeding 286,000 units. In large part this was due to the enormous popularity of the CR-V.
Since September and October 1997, when the Accord and its derivatives went on sale in the Japanese market, Line Two utilization has risen to more than 80%. And production of the car, after a slow start in July and August, rose to 11,000 units in October, 12,600 in November and 11,500 in December, or 60% of output over the three-month period.
Production has remained close to those levels ever since, aided by the launch of the U.S. model.
Honda began planning for the Accord launch here in June 1996, a full year before production startup. Then in late December, the company began installation and testing of new tooling and equipment while the plant was shut for Japan's eight-day New Year's holiday. None of the big stuff. That would wait until the end of April 1997, when the plant was closed for 10 days to mark the spring "Golden Week" holiday.
For the next four months through April 26, trials were conducted on 20 key assembly processes in a small, off-line test plant within the Sayama complex. These tests, covering both assembly and precision fitting, involved doors, the trunk and hood, the powertrain and the suspension, major components that differed from those in previous Accords or other models produced on the line.
Full production trials began five weeks after Golden Week on June 9. And for the next five weeks until July 15, the company ran approximately 10 production tests - involving three to five cars per test - slowing down the line to work out any wrinkles.
Plant official Hitoshi Tanaka estimates production "losses" of 20 to 30 units per trial, thus a maximum of 300 for the ramp-up. Losses, more precisely "lost opportunities," are vehicles not built due to slow line speed or downtime resulting from the ramp-up and include empty carriages moving through the line.
Mr. Tanaka, who is chief engineer of the plant's body assembly planning department and was deeply involved with the Accord launch, explains, "The reason lost vehicles' were so low is that we did most trials off-line."
Finally on July 21, production got under way. Honda built 10 Accord sedans on the first day. By July 28 (Day Five), the number had risen to 100. Five business days later on Aug. 4 (Day Ten), output was up to 130, the com-pany's target. For the rest of the month, production volumes fluctuated between 130 and 150 units, enabling Honda to build up an inventory of 2,500 to 3,000 cars in preparation for the model's early September sales launch.
Despite the differences in the two Accord launches (at Sayama and Marys-ville), there are many important similarities. Among them: tooling and equipment were installed throughout the year - on weekends, on third shifts and during annual plant holiday shutdowns. Moreover, both facilities spent nearly half a year on pre-production and both relied heavily on production specialists to assist with product planning. In neither case was there an increase in plant size and manpower.
In Japan, Motoatsu Shiraishi, managing director in charge of production at Honda, credits the Japanese Accord's super-quick tachiagari, or ramp-up, to the company's "ultra-lean" manufacturing concept. And lean production at Honda, more than its domestic rivals, is driven by acute space shortages in land-poor Japan. The site on which the Sayama plant was built spans only 95 acres (38 ha).
As a result, Honda was one of the first automakers in Japan to embrace off-line
assembly of key modules and components - instrument panels, doors, steering wheels and brakes.
And in no place is this more apparent than at Sayama. Now in its 35th year of operation, the plant is cramped, spartan and well-worn, a no-frills facility with one of the lowest automation rates of any large auto plant in Japan. In fact, final assembly automation stands at only 6% and is limited to strenuous operations such as seat installation, tire and wheel positioning and bolt-tightening, and rear suspension placement.
"We couldn't vary our product mix if we had overdone automation," says Honda's Tanaka. Merrill Lynch Japan's Takaki Nakanishi adds: "The beauty of Sayama is its flexibility. This enables Honda to shift production quickly, efficiently and cost-effectively."
Flexible deployment of the plant's
final assembly labor force - numbering 2,500, or 40% of the total - allows the company to build virtually any number and variation of models without having to make a major investment in facilities. "This feature is invaluable during unstable market conditions," insists Mr. Nakanishi.
In fact, tooling costs for the 1997 Accord launch came to only $52 million (6 billion), based on best estimates by analysts. Included were modular assembly lines for front and rear suspensions along with new welding jigs and stamping dies.
The bottom line: Both Honda and Honda of America win big where it counts . . . on the bottom line...
Read more about:
1999About the Author
You May Also Like