Honda Digs Deep to Upgrade Ohio Plants for AccordHonda Digs Deep to Upgrade Ohio Plants for Accord
The ’13 sedan and coupe brought about a number of changes to the Japanese auto maker’s U.S. manufacturing processes, ranging from a new 200-ft.-long stamping press at Marysville to a new transmission assembly line for Russells Point.
January 14, 2013
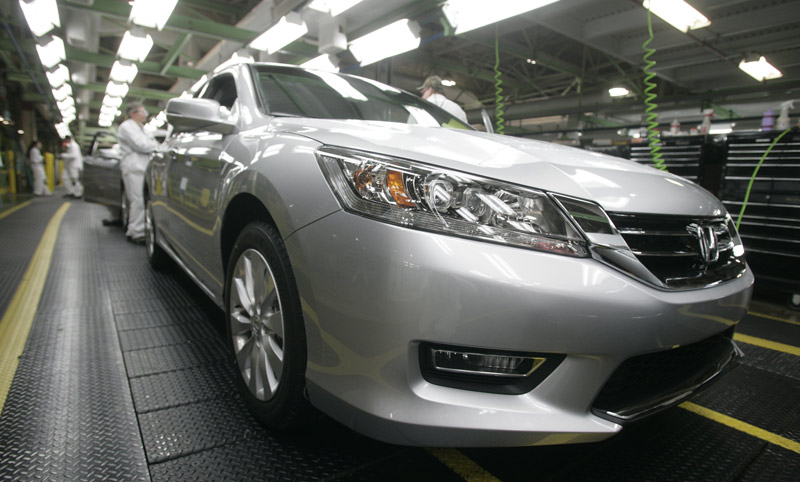
MARYSVILLE, OH – The new, ninth-generation Accord not only represents a major change to Honda’s high-volume midsize car but also is responsible for a transformation in a number of manufacturing processes at the auto maker’s Ohio plants, where the model is built.
They include the Marysville assembly plant, Anna engine facility and Russells Point transmission-manufacturing operation.
Most Accords sold in the U.S. for the past 30 years have been assembled at Honda’s Marysville facility, located just outside Columbus. But the contemporary exterior and interior designs of the ’13 sedan and coupe models, on sale now, called for creative solutions to accomplish the necessary factory upgrades to build the cars.
A new $64 million, 18-shot-per-minute B-line servo press, for instance, was installed last year that allows for the deep-draw stampings of the sheet metal that enhance the car’s exterior styling.
However, before installation of the machinery could proceed, Honda literally had to dig deep, excavating a 30-ft. (9-m) deep pit that is 100-ft. (30-m) wide and 200-ft. (61-m) long to house the press.
Excavation of the pit had to be carefully choreographed so as not to disrupt production of the ’12 Accord and Acura TL. Jeff Tomko, Marysville plant manager, says it took Honda four months just to engineer a way to prevent dirt or concrete falloff while digging the pit.
“This is an existing building; there’s production all around us, and we (enclosed an) area to be able to drop this press in,” Tomko tells WardsAuto, which was given unprecedented access to Honda’s Ohio manufacturing operations.
Preparation for the installation of the new servo press, which included 1,250 truckloads of concrete, took six months.
A smaller dig was undertaken for three new ultrasonic knife machines that cut the notches on the backside of the Accord’s seamless instrument panel, allowing the airbag to deploy.
Because of the vibration inherent in an auto factory from stamping presses and welding lines, each ultrasonic knife required a seismic isolation base 6 ft. (1.8 m) below ground. The cutting machines sit on a gas box with isolator pads underneath.
“These are the most accurate pieces of equipment we have in production anywhere in Honda,” says Rob Howells, staff engineer overseeing maintenance and engineering in Marysville’s forming department.
The ultrasonic knives have a tolerance of plus-or-minus 0.002 ins. (0.06 mm). Measuring sensors determine the thickness of the IP cover foam, which is about 0.017 ins. (0.44 mm). A mill cut is made to thin the material, and data from the sensors correctly positions the knife that is almost invisible to the human eye.
The knife makes three small cuts, one in the middle and two on each side, that allow the IP’s skin to rip down the center, two doors to open and fold back and the airbag to deploy.
Honda’s in-house engineering group designed the machine, and Marysville is the auto maker’s first North American plant to use it.
Howells says an earlier version of the ultrasonic cutter used at Honda’s Suzuka, Japan, factory, performs only the mill cut that thins the plastic for the IP in the auto maker’s N Box, Japan-market Kei car. The Sayama, Japan, plant, which also produces the Accord for North America, uses the current-generation cutter.
Other updates to Marysville for the ’13 Accord include:
A new multi-aiming station with a visual target board that uses radar-reflective prisms to confirm the car’s optional safety technology, such as lane-departure warning, is functioning properly.
Additional ergonomic equipment in vehicle assembly, including assist devices that reduce the strain of overhead work for employees.
Eight new robots in the welding department, due to the increased amount of high-strength steel in the ’13 Accord compared with the ’12 model.
Additionally, Marysville will add production of the new 2-motor ’14 Accord Hybrid later this year. The auto maker is expanding the plant by 95,000 sq.-ft. (8,826 sq.-m) to accommodate a longer main assembly line and house parts for the new hybrid.
Anna Engine Facility
Honda’s 27-year-old engine plant in Anna, 50 miles (80 km) from Marysville, also has undergone significant changes for the introduction of the ’13 Accord, in this case largely due to the car’s all-new 2.4L 4-cyl. gasoline direct-injected mill.
Anna is Honda’s largest engine facility globally, with an installed annual capacity of 1.2 million units, and is the first of the auto maker’s engine-production sites to assemble the new 4-cyl.
“The displacement remains the same as the prior model year, but the engine is completely new save for a few bolts,” says Denis Kovacs, senior staff engineer-new model at Anna.
While Anna’s Line 1 still is exclusively dedicated to building 4-cyls. for the Accord, as well as the Honda CR-V cross/utility vehicle, the auto maker now mixes 4-cyl. production into the formerly V6-only Line 2.
“This was a big challenge for us, but it gives us a lot more flexibility for market demand,” says Tony Fullenkamp, department manager-engine assembly, referring to shifting consumer preference in recent years toward cars with smaller, less-thirsty engines.
The addition of the new 4-cyl. to Line 2, a process that took more than a year, also allowed Honda to update machinery and introduce more automation. “Automation helps improve some of the overall accuracy and labor-intensiveness” of manufacturing the 4-cyl., Fullenkamp explains.
One example of this is the automatic tappet-set robots. “The robots go in and adjust the valve clearance and rotate the engine,” he says. “On the older lines (1 and 3), it’s being done by hand.”
Automatic tappet set not only bolters manufacturing accuracy but also improves ergonomics for employees, who now use just one wrist movement to set the tappet. Honda also added a spur conveyer in the shape of a horseshoe to lengthen Line 2 to accommodate the new 4-cyl.
With the mixing of the 4-cyl. and V-6 Accord engines, Fullenkamp says Line 3 workers were moved to Line 2 to learn specifications for the new 4-cyl. while still working on Line 3. “It was a big challenge,” he says. “We’d take associates over to Line 2, have them run for six hours – we call that ‘human flex’ – and then they’d go over (to Line 3).”
Fullenkamp describes it as a win-win experiment, noting employees liked the variety and it allowed Honda to meet Line 2 requirements faster.
Although the next-generation Accord is in production, updates to Anna are not yet completed. Starting in August, the plant will lathe, heat-treat, grind and subassemble the pulleys for the ’14 Accord’s continuously variable transmission. American Axle will forge the shaft pulleys and TFO Tech will provide the movable pulleys for Anna.
The ’13 model’s CVT currently is assembled in Russells Point using sub-assemblies sourced from Japan. To accommodate the pulley output, Anna has moved brake-disc production that was in-house to an affiliate company in Michigan.
As of late September, heat-treat machines for the pulleys had been installed and installation of air conditioning and power was under way, ahead of the expected equipment installation this month. A pilot line for the pulleys has been in place at Anna since August 2012.
Honda has tried to localize more components with the introduction of the next-generation Accord, and Don Wiktorowski, CVT pulley project leader, says during CVT forging trials Anna has been using steel from Michigan-based Gerdau, rather than from Dido, its usual steel supplier in Japan.
“We’re still in testing, but so far everything’s looking really well. They’re matched up really closely to the Dido material,” he says of the U.S.-made steel.
CVT pulley final mass production should begin in June, and by August shipments from Anna to Russells Point are set to begin. Anna temporarily is making transmission-case castings for the new CVT at Russells Point, but by the end of the year that production will transfer to the transmission plant.
When that happens, Anna will replace some of its die-cast equipment, much of it at least 25 years old. The machine upgrades are expected to reduce energy usage and add automation, Anna Plant Manager John Spoltman says.
Russells Point Transmission Plant
Just 20 miles (32 km) from Anna, Honda’s transmission plant saw the most ambitious upgrade of any of the auto maker’s Ohio Accord facilities.
Russells Point was expanded to manufacture the car’s CVT, Honda’s first non-hybrid CVT to be offered on a North American model and the first such transmission the auto maker has produced in the region.
Honda invested $120 million in Russells Point for the new transmission, $70 million of which financed the cost of construction for an additional 200,000-sq.-ft. (18,581-sq.-m) of space to accommodate the assembly line.
The remaining $50 million was spent on a 75,000-sq.-ft. (6,968-sq.-m) expansion, currently under construction, to house additional aluminum casting for the new CVT line.
The CVT assembly line also introduces some new manufacturing guidelines for Honda in North America, notably regarding noise levels and cleanliness. The assembly area is certified ISO Level 8, not quite a microchip-manufacturing level of clean and quiet but a step above the typical auto manufacturing facility ISO Level 9 certification.
Helping keep the area quiet, and comfortable, is a drop ceiling, a burgeoning feature for Honda plants, including its transmission facility in Tallapoosa, GA, and some factories in Japan and Indonesia.
“The drop ceiling helps us control the temperature in this room and also it’s kind of sound-deadening,” says Gary Hand, vice president for Russells Point. “The design is a little bit more costly, but long-term we think it has good benefits.”
The ceiling is painted white, and combined with skylights helps brighten the assembly area and allows Honda to reduce artificial lighting.
As with changes to Marysville and Anna, Russells Point has increased its automation.
As a countermeasure on the new CVT line, sensors inside equipment detect the presence of parts, so “we don’t have to rely so much on an associate putting something in the correct order or the correct way,” says Justin McAuley, Line 3 quality leader at Russells Point, noting the sensors also can detect a wrong part.
Honda introduced the sensors several years ago for assembly of its 5-speed automatic transmission, but has increased their usage and made them CVT-specific for the new transmission.
“We have more automation on this line than we do on the other automatic-transmission line,” McAuley says. “Some of it is due to the higher amount of precision items that go along with the CVT.”
However, the increase in automation has not reduced the need for worker training, even though there are fewer processes in CVT production than with a step-gear automatic.
Because the ’13 Accord’s automatic transmission is new to Honda in North America and is a more finicky design compared with Honda’s 5-speed automatic, more time has been spent training engineers and plant workers.
“There’s a lot of select-fit items, a lot of really” precise machining involved in CVT production, McAuley says. For instance, early on in the assembly process, workers must measure to make sure pullets align horizontally and that “there’s no strange torque on the belt.”
At full capacity, Russells Point can churn out 1,250 transmissions a day with two shifts. The plant initially received 15,000 CVTs from Japan while the second shift ramped up in late summer/early fall. Today, 100% of the ’13 Accord non-hybrid CVTs come from Russells Point, Honda says.
About 60% of the CVT line employees were hired from within Honda, while 40% are new hires. “We try to keep a good mix (of new and experienced workers on the line),” McAuley says, in order to maintain quality.
Honda has roughly 50 workers per shift on the new CVT line at Russells Point. The ’12 Accord’s 5-speed automatic line maintained slightly more employees because of the number of processes involved in assembling the step-gear automatic.
A second CVT assembly line is being added at Russells Point, as well as new aluminum die casting and machining operations.
You May Also Like