Hyundai Boosts Fortunes of Alabama Capital
Cumulative investment in the 6-year-old complex approaches $1.6 billion and will reach $1.7 billion when remodeling of the older of two engine shops is completed next spring.
October 6, 2011
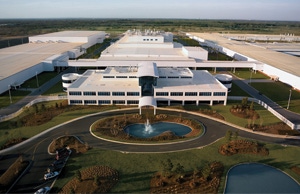
MONTGOMERY, AL –Ten miles due south of Montgomery’s storied historic district, Hyundai Motor Mfg. Alabama has made some history of its own since setting up shop in 2005.
Hyundai was the first Korean auto maker to open a plant in the U.S. and, until the recent arrival of German steel maker ThyssenKrupp, the largest foreign manufacturer of anything to settle in Alabama.
Hyundai has been a boon for the state’s economy, creating more than 30,000 direct and indirect jobs, including those at suppliers.
Ellen McNair, senior vice president-corporate development for the Montgomery Area Chamber of Commerce, was a key player in the yearlong selection process from which Alabama’s capital city was chosen from among 100 candidate locations. She says Montgomery offered a “perfect” site: nearly 2,000 acres (809 ha) of farmland near an interstate highway and the CSX railroad.
“And because of the early successes of Mercedes and Honda,” she says, “we could say what Alabama workers ‘can do,’ not what they were ‘going to do.’”
Mercedes-Benz arrived in Tuscaloosa County in 1996, followed five years later by Honda in Lincoln, 40 miles (64 km) east of Birmingham, the state’s largest city.
Hyundai’s choice of Montgomery was announced in April 2002, and the first car rolled off the line in May 2006.
Montgomery is Hyundai’s second try at building cars in North America. In 1989, the auto maker opened an assembly plant in Bromont, Quebec, Canada, 50 miles (80 km) east of Montreal. The $388 million plant, which built an earlier-generation Sonata, shut down after four years because of insufficient demand. Not so this time round.
Front of Hyundai Alabama plant.
The Montgomery plant, with a state-supported training center included in its more than 3 million sq.-ft. (279,000 sq.-m), currently builds nearly 1,300 Sonata and Elantra sedans daily with 2,500 mostly hourly workers.
Ashley Frye, Hyundai-Alabama vice president-manufacturing, says the sprawling facility differs in several key respects from the auto maker’s Asan factory in South Korea, which had been the base plant for the Sonata when the decision was made to build the car in the U.S.
Among other things, Frye explains, the Montgomery plant is more spacious, with wide aisles that make in-plant parts delivery easier.
And there’s none of the line-side clutter seen in many older assembly plants. This is by design to foster higher quality. “If everything is neat and orderly, it’s easier for team members to work accurately on a consistent basis,” Frye says.
Cumulative investment in the complex approaches $1.6 billion and will reach $1.7 billion when remodeling of the older of two engine shops is completed next spring.
3-D view of plant with stamping and welding shops on left, followed by paint shop (behind administration building in front), trim and final assembly shop, two engine plants to right.
Other plant facts:
It currently makes three Sonata and two Elantra models: the Sonata GLS, SE, and Select Limited (the latter two available in both turbo and non-turbo versions) and the Elantra GLS and Limited. Both marques are sold in the U.S., Canada and Puerto Rico.
It takes 17 hours to produce a car from welding to final inspection, including nine hours in the paint shop and six in final assembly. Output is 75 units per hour.
A large display in the operations center shows all vehicles ‘in process’ moving from station to station through the plant. Included are 300 in final assembly, 600 in the paint shop and 200 in the body assembly/welding shop.
The first-time ‘through’ rate is 99.6%. About 10 vehicles are pulled off the line daily for repairs.
Robots assembling body shell.
The plant runs on two 10-hour shifts Monday through Friday and, depending on demand, two 8-hour shifts on Saturdays.
Average hourly wage is $21-$22.
Breaking down staffing by shop, 1,200 workers are in general assembly, 300 in painting and 100 in body assembly/welding. The remaining 700 are involved in engine production, stamping, final inspection, maintenance and logistics. There are about 200 temporary employees.
The stamping shop is equipped with two 5,400-ton (4,900-t) IHI presses. Dies are changed in less than five minutes, with stamped parts going to an automated warehouse inside the shop.
From the warehouse, stamped pieces are transported to the body-assembly shop where 251 spot-welding robots automatically apply all of the 2,100 spot welds, Hyundai officials say.
White-body-inspection line before release to paint shop.
Nearly one-third of the shop’s robot workforce form a large general welder that joins side panels, floor, trunk-shell and roof cross-members. Door frames, side panels and other key components are welded together on sublines in the shop. Doors, hoods, trunk lids and hinges are attached manually before the completed body is released to the paint shop.
Including material-handling units, the shop uses a total of 280 robots. Combined floor space of the body-assembly and stamping shops is 489,743 sq.-ft. (45,500 sq.-m).
Upon entering the 336,926-sq.-ft. (31,300 sq.-m) paint shop, each car is washed, then coated with a crystalline-phosphate solution to ensure adhesion before electrodeposition, or electroplating. The car afterward goes to the first of five ovens that rotate it 360 degrees to prevent air pockets from forming.
Sealant is applied before the car proceeds to a second oven, followed by more light sanding, then the surface coat and the third oven and, finally, two top coats, both water-based along with the surface coat, and two more ovens.
Regenerative thermal oxidizers are used during the drying process.
Car being dipped and rotated in paint shop.
Ten vehicles can be seen passing through a brightly lit inspection line where even the tiniest blemish is spotted by one of 16 trained inspectors. About 30 of the paint shop’s 300 workers are dedicated inspectors. Including in-line inspectors involved in touchup and sanding, the total reaches 90.
The paint shop has four miles of conveyors and 88 robots, including 64 painting robots and 24 sealing and deadening units. It handles nine colors.
Twelve lines snaking through the final-assembly operation include two chassis, five trim, four final-assembly and one automated testing and final inspection. Engines, front and rear suspensions, doors and tire-and-wheel sets are assembled on sets of sublines.
Each main line consists of 20-25 stations, for a plant total of 260, and employs an average 50 workers per shift. The shop’s total workforce, excluding maintenance personnel, is 600 per shift.
The first and second chassis lines each have 24 stations, the first three trim lines have 20 apiece and each of the final-assembly lines have 26. On the third trim line, workers attach the front and rear fascia while a robot installs the cockpit module.
Paint robots at work.
The final-assembly shop employs 11 robots: One each for cockpit module, battery and spare-tire installation; two for fitting the windshield and rear window; two that apply adhesive; two that install the front seat; and two that tighten the front-end module into place.
The car moves through the chassis line by electrified overhead monorails, then meets the engine/transmission assembly operation running underneath on height-adjustable “skillets,” which then lift the engine/transmission assembly, exhaust system, chassis and gas tank into the car’s body, where it is bolted by line workers.
Unlike Nissan’s plants in Canton, MS, and Smyrna, TN, Hyundai has no plans to introduce a “kitting” operation or bring suppliers in-plant to make modules. Most modules, the main exception being doors, will continue to be delivered from Hyundai’s main suppliers, many of which are located within 10 miles (16 km) of the plant.
Front- and rear-wheel alignment is checked on drums inside the plant at speeds up to 70 mph (112 km/h), after which each car is driven over a 2.3-mile (3.7-km) test track to check mainly for noise, then readied for shipment to Hyundai’s North American dealers.
Team member assembling 2.4L Theta engine
The final-assembly shop covers 857,385 sq.-ft. (79,651 sq.-m), one-fourth of the plant’s total floor space, with loading bays built around the perimeter for easy access by suppliers.
Team members of the door subline manually remove doors at the start of the first trim line. The doors then are transported by a hook-type conveyor to a subassembly line where power windows, locks, door handles, speakers and other components are attached. Two workers man each of the line’s 20-plus stations, one on each side for left and right doors.
The assembled door is taken to the end of the trim line, where it is manually reattached with the aid of a lift-assist device.
The 708,337-sq.-ft. (65,800 sq.-m) engine plant has two sections. The newer one, which opened in September 2008, makes 4-cyl. Theta engines for both Hyundai’s Montgomery plant and the Kia Motors Mfg. Georgia facility in West Point, GA.
Final inspection line.
The older plant, in operation since 2005 when the first Sonata rolled off the line, is being renovated to make 4-cyl. Nu engines. The plant had produced the Lambda V-6 engine for the Santa Fe before the model was shifted to West Point in September 2010.
Both Nu and Lambda engines, built respectively for the 1.8L Elantra and 3.6L Santa Fe, currently are imported from South Korea. When the $163 million renovation is completed next spring, capacity of the older Montgomery engine plant will increase to 300,000 units including 150,000 Nu engines. Total plant capacity will grow to 660,000 units.
Automatic transmissions are trucked from Powertech America’s West Point plant 90 miles (145 km) southeast of Montgomery, where they are mated to Sonata and Elantra engines inside the No.2 engine plant, then transported by trestle across a narrow roadway to the final-assembly shop’s chassis line.
Key suppliers include makers of seats, cockpits, front-end modules and fascias.
<link rel=
">
Hyundai Mobis, six miles (10 km) from the plant, makes cockpit modules, front and rear suspensions and door trim, along with supplying painted bumpers.
Hyundai’s Korean supply base has invested an estimated $500 million in Alabama manufacturing operations. The auto maker claims that its NAFTA content exceeds 65%.
About the Author
You May Also Like