Data Intelligence Key to Unlocking Auto Industry InnovationData Intelligence Key to Unlocking Auto Industry Innovation
To meet the promise of smart manufacturing, we need a deeper understanding of topics such as data in manufacturing, manufacturing robustness and the use of simulation for discovery.
July 8, 2022
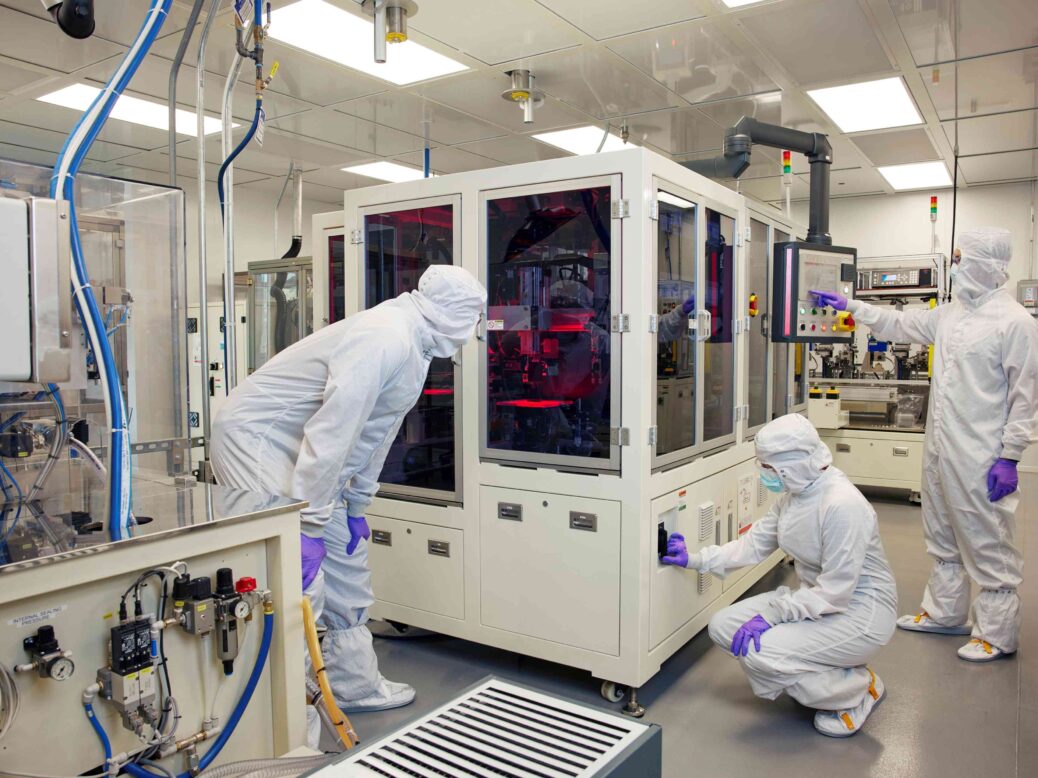
From autonomous vehicles to electrification, the need for continuous innovation in automotive manufacturing is more urgent than ever. But with products, capabilities and materials evolving daily, the demand can quickly outpace the supply.
To thrive in this landscape, researchers in the manufacturing space need to be agile, responsive and collaborative. Innovating isn’t enough; we need to continuously accelerate our efforts.
An Open Model
Today, many manufacturers, including General Motors, embrace an open innovation model. By combining off-the-shelf technology with proprietary concepts and processes, manufacturers can increase the speed of innovation while maintaining quality and delivering on timing.
By eliminating the need to invent everything, an open innovation model allows teams to focus attention at the points where existing technologies can intersect with unique and non-obvious applications. Doing so increases the company's potential to differentiate while saving costs and resources.
Industry is rapidly evolving; in 2021, GM announced it would invest an additional $35 billion globally in autonomous and electric vehicles through 2025 as part of its path to an all-electric future. Even with an open innovation model, manufacturing research professionals need to constantly increase the pace of innovation. Our role is not just to keep up with the vision for the future, but also lead the industry.
The Big Data Revolution
Big data is transforming manufacturing, and the automotive industry is no exception. As R&D accelerates toward an electric, autonomous future, intelligent use of data in the manufacturing space – or smart manufacturing – is one of the keys to unlocking untapped potential.
Smart data offers several promising avenues for auto manufacturing. The first is improving the quality of processes. At the micro level, we can use data to analyze and avoid potential pitfalls, achieving a previously unattainable level of process control. At the macro level, data can be used across the operation or the whole enterprise to improve operational efficiency.
Another area of potential is tapping into the promise of analytics to optimize research. Data gathered during research can uncover underlying truths about processes and operations that aren’t obvious from observation alone. Acting on these insights can, and will, drive rapid change in automotive manufacturing.
All the benchmarks we strive for in electrification, autonomous vehicles and sustainability will be influenced by the data we gather. But to get there, we need to improve our processes for collecting and extracting information. While we have the means to gather vast swaths of data, our industry currently lacks standardized methods to sort and apply it.
From Data to Information
Smart manufacturing has the potential to revolutionize our industry, but harnessing it is our next major challenge. The path from concept to implementation can be a long one.
While today feels like an exciting and unique space in manufacturing research, it is the culmination of decades of work. Researchers began developing neural networks in the early 1970s. Today, deep learning and convolutional neural networks play a vital role in monitoring and maintaining production quality in manufacturing plants. But it’s only in the past decade that we’ve developed practical models for applying neural technology in the automotive industry.
In the next five years, we can expect an explosion of data applications in automotive manufacturing. But to transform raw data into actionable insights, we need to create efficient ways to identify the subsets of data that can improve our processes and products. That means turning our research focus to data processing and standardizing the equipment and methods we use to extract information to ensure we can quickly and effectively deploy new intelligence.
Spurring Innovation in Research
Recently, Purdue University hosted the 50th Annual North American Manufacturing Research Conference (NAMRC). The longest-running forum for applied research and industrial applications in manufacturing and design, it brought together academics in engineering and professionals in the manufacturing research space.
Summits such as NAMRC are vital. Just as we rely on outside technology to increase the pace of research development through open innovation, we rely on the academic community for in-depth, focused research into priority areas.
About 10 years ago, GM started working in ultrasonic welding. At that time, there was almost no scientific literature on the topic – a significant roadblock to applied research. As we presented our work to the academic community at conferences, we were able to stimulate new attention to the topic. A decade later, new papers on ultrasonic welding are released almost weekly.
Jeffrey Abell GM 2022
The level of innovation that automotive manufacturing demands today will require academic and industry professionals to examine the same problems and work hand-in-hand toward solutions. To meet the promise of smart manufacturing, we need a deeper understanding of topics such as data in manufacturing, manufacturing robustness and the use of simulation for discovery.Through forums such as NAMRC, professionals in the manufacturing research space have the opportunity to influence, inspire and provoke new research into the intelligent use of data in manufacturing and, in doing so, accelerate our industry into the future.
Jeffrey Abell (pictured, above left) is chief scientist for global manufacturing and director of manufacturing systems research at General Motors. He is responsible for global manufacturing research focused on vehicle electrification, lightweight systems manufacturing, automation and smart manufacturing.
About the Author
You May Also Like