Henkel’s LOCTITE SI 5972FC Slashes Time for Sealing Auto Electronic ComponentsHenkel’s LOCTITE SI 5972FC Slashes Time for Sealing Auto Electronic Components
Henkel’s LOCTITE SI 5972FC optimizes automotive electronic component manufacturing by accelerating the process of electronic module sealing.
January 29, 2024
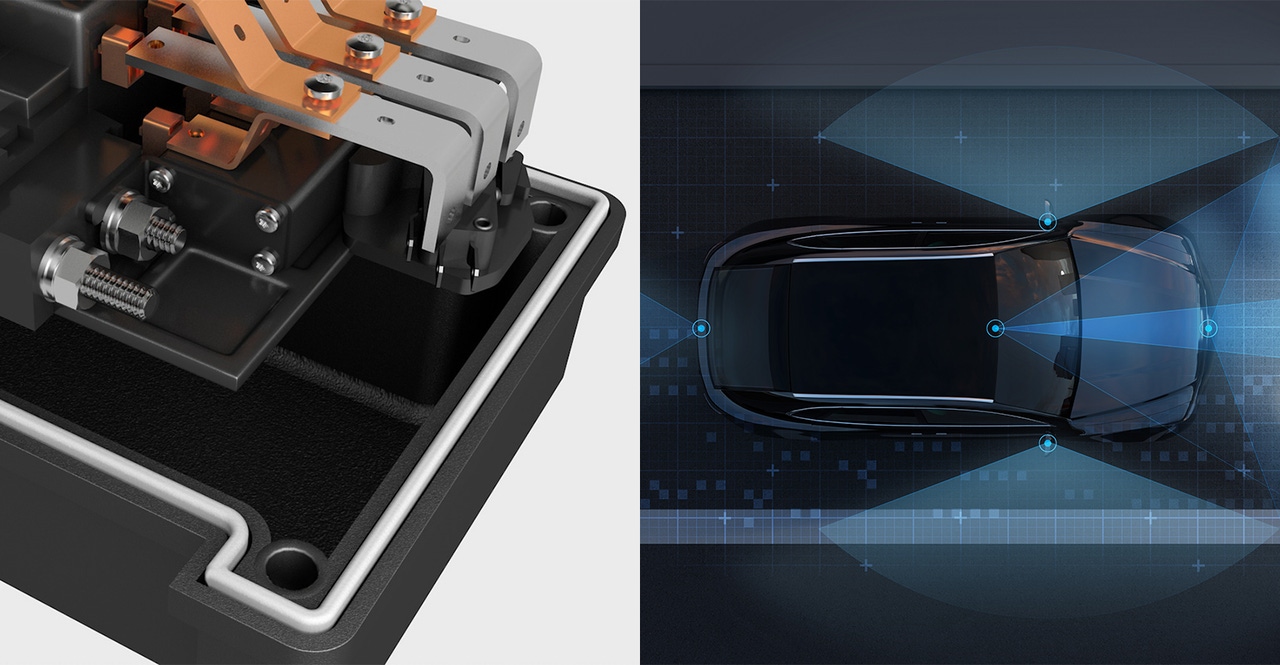
Growing demand for highly reliable automotive electronic components means every aspect of design and manufacturing must be optimized. Henkel’s LOCTITE SI 5972FC significantly reduces cycle time by providing a robust assembly seal capable of passing a leak test without prolonged time for cure time. This faster processing allows shorter staging times and reduces the need for excess floor space in production facilities that is usually occupied by racks of parts waiting to be tested.
Thanks to its unique formulation, this one-part, silicone form-in-place gasket (FIPG), can pass a 3-psi leak test immediately after assembly. As a result, the need for time- and space-intensive staging is eliminated, reducing complexity and speeding production.
Typically, room temperature vulcanizing (RTV) curing occurs via moisture absorption over a period of hours to days. During that time, assembled parts are staged in racks, requiring valuable floor space that could be used for other purposes.
In addition to increasing manufacturing efficiency, LOCTITE SI 5972FC is formulated for non-corrosive outgassing and low volatility (D4-D10 <0.1%), making it ideal for sensitive electronic components. With exceptional adhesion to diverse substrates, including aluminum and glass-filled plastics, the technology is ideal for applications such as: Electronic Control Units (ECU), Bussed Electric Centers (BEC), Battery Disconnect Units (BDU), Electrical Power Steering (EPS) Power Packs and ADAS (Radar) components.
Blowout Performance
During pressure testing, blowout resistance was measured by the ability of the material to withstand air pressure at both a 1 mm gap and a 2 mm gap for greater than 60 seconds. In both instances, LOCTITE SI 5972FC passed a 3- psi leak test immediately after end-of-line assembly is completed – thanks to a significantly faster rate of strength build-up compared to a comparative product solution.
DSGN0034626_5972 FC full cured strength chart
Delivering Safer, More Sustainable Components
As a champion of sustainability, Henkel continues to develop solutions that reduce environmental impact across the value chain. Through its tin-free catalyst and alkoxy curing system, LOCTITE SI 5972FC meets European REACH regulations, while reducing energy use and carbon emissions through avoiding the need for curing ovens. EU REACH regulations, which require D4, D5 and D6 siloxanes to be < 0.1 wt.% in composition, are expected to impact North America in coming years.
LOCTITE SI 5972FC features key benefits in relation to form stability, dispensability, aspect ratio, cure rate and post-dispense leak testing.
DSGN0034626_Technical chart_0
Learn more about LOCTITE SI 5972FC in our product information sheet or get in touch with Henkel directly here.
770x400px_v2.jpg
About the Author
You May Also Like