Your Car Built for You – While You WaitYour Car Built for You – While You Wait
The first street-legal 3D-printed cars from Local Motors are expected within 24 months. Renowned Ford GT designer Camilo Pardo is lobbying to design one.
August 6, 2015
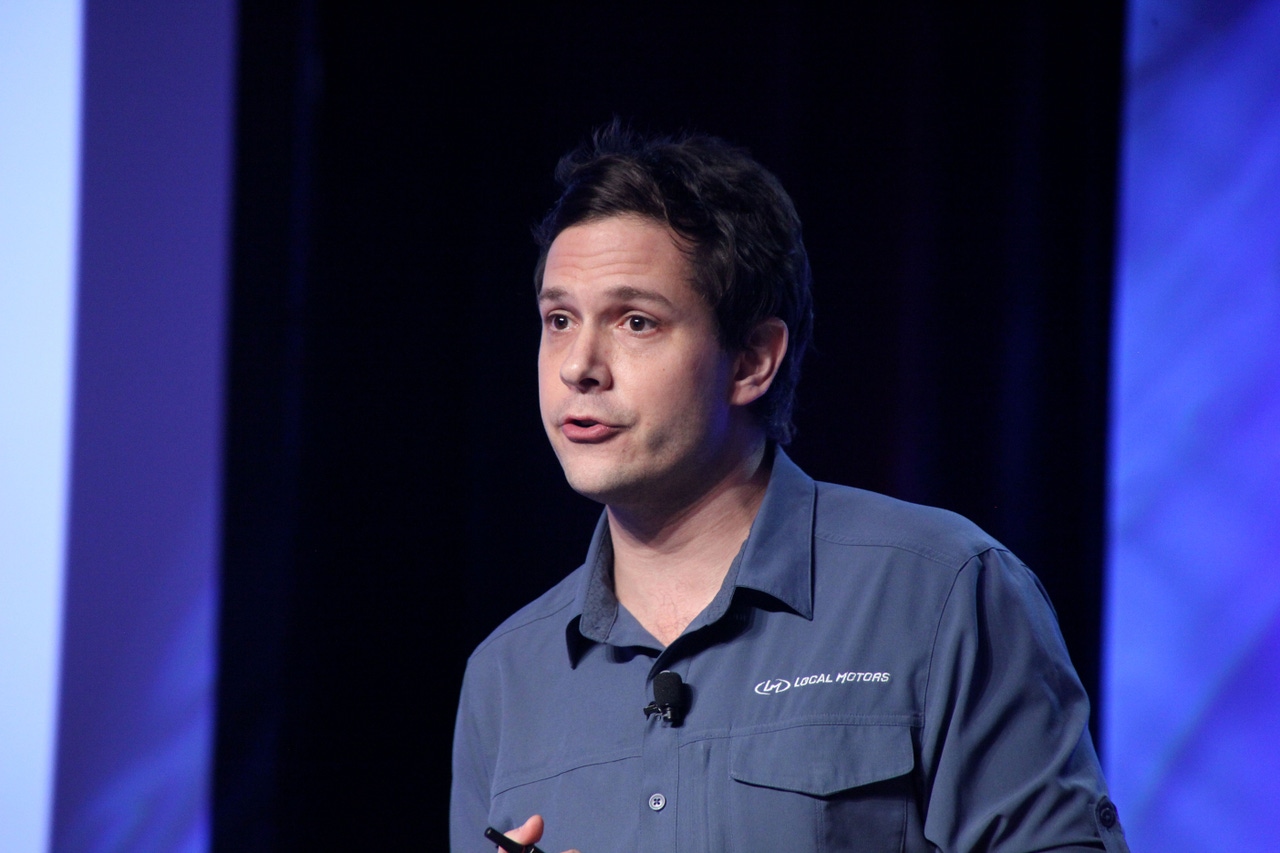
TRAVERSE CITY, MI – Europeans like to order their cars and wait for weeks or even months for the factory to build them. Americans want to find their cars on dealer lots and buy them right now.
Local Motors will split the difference: It will build a car for you – while you wait.
The radical automotive designer and direct digital manufacturer that built the world’s first fullsize 3D-printed car is using crowdsourcing principles as the foundation of its new-age business model.
The company has collaborated in numerous transportation-industry projects to demonstrate its cutting-edge process to build low-volume, 3D-printed vehicles in small “microfactories,” and now is on the cusp of producing its first road-going car.
Local Motors is so painfully cool and full of potential that renowned automotive and industrial designer Camilo Pardo (the fellow who penned the second-generation Ford GT sold in 2005-2006), prods fellow Management Briefing Seminars panelist Justin Fishkin, Local Motors’ chief strategy officer, to let him design a vehicle for the company. With Pardo, it’s usually the other way around.
Fishkin tells attendees here that after settling on two designs from about 200 crowdsourced submissions from 30 countries, Local Motors plans to build its first street-legal car within the next 24 months.
What’s more, the direct digital 3D manufacturing process to build the fullsize car is under such rapid continual improvement that it now will be able to print the car while you wait at one of the 50 microfactories it intends to have operating worldwide.
This is more than vaporware: Phoenix-based Local Motors got plenty of exposure in the mainstream press when it built the world’s first drivable 3D-printed car last September. It produced another on the display floor of the North American International Auto Show in Detroit earlier this year.
Fishkin says improvements to the digital manufacturing process – using carbon-fiber-infused ABS plastic to build, in layers, the structure and bodywork of the vehicle – has cut the time needed to produce an entire car from 180 hours to just 44. That efficiency gain was made during the short 3-month span between the printing of its first car in September and the subsequent model at the Detroit auto show in January.
Local Motors’ digital design-and-build process will be able to bring vehicles to market five times faster than the traditional auto industry can manage, and at 100 times lower cost, Fishkin contends.
“We’re not tooling up to make a vehicle that works everywhere,” he says. By building vehicles designed for local preferences and in small batches, Fishkin adds, the company can be infinitely more flexible than today’s automakers, which have to design and build vehicles for mass production in high-cost, centralized factories.
The executive doesn’t provide any details on what a built-while-you-wait vehicle might cost. But the company is completing new microfactories in Knoxville, TN, and National Harbor, MD, that will be onstream this fall, and Fishkin says it is on track with its plan to have 50 microfactories globally in the future.
The first car set for production is the Project Reload Redacted (hey, it’s a crowdsourced thing), which will be offered in about 10 body styles and with a couple of powertrain and wheel/tire choices.
In all, the car consists of only about 50 or so major components, Fishkin says. If the owner gets tired of the car’s styling or sees an upgrade he likes, it can be returned to the factory to be reworked.
There, the components can be stripped and the body/chassis melted down, with about 80% of the carbon-fiber-reinforced plastic reusable.
About the Author
You May Also Like