Looking Inward
Rhodia Engineering Plastics has developed a new material that the company will use to pursue North American vehicle interior applications. The Lyon, France-based polyamide thermoplastic producer, a division of the Rhodia Group chemical company, currently focuses its automotive business on underhood applications. We have not been a major interior player, Chad Waldschmidt, Rhodia North America automotive
June 1, 2003
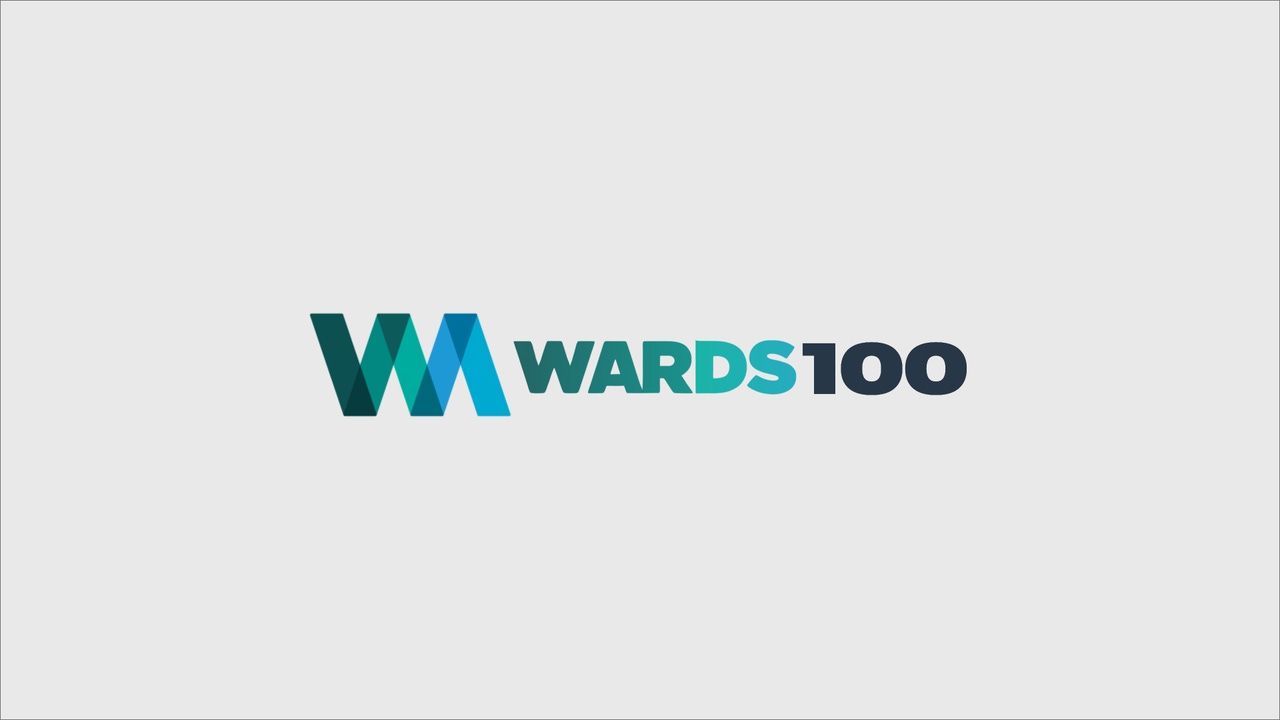
Rhodia Engineering Plastics has developed a new material that the company will use to pursue North American vehicle interior applications.
The Lyon, France-based polyamide thermoplastic producer, a division of the Rhodia Group chemical company, currently focuses its automotive business on underhood applications.
“We have not been a major interior player,” Chad Waldschmidt, Rhodia North America automotive director, says at the company's North American application and technology development center in Farmington Hills, MI.
“We have had various applications that we've been involved in. There are areas where we've been present. But this is really a big thrust for us into the interior.”
The Technyl Alloy resins are a new thermoplastic family of Polyamide (PA) and Acrylonitrile Butadiene Styrene (ABS) alloys.
A proprietary technology enhances the combination of PA/ABS, Rhodia claims, to provide advantages for molded plastic parts versus components made from traditional polycarbonate, PC/ABS and PC/polybutylene terephthalate.
Rhodia isn't the first to bring a PA/ABS to market. But previous attempts have not met expectations. “We think the key here is being able to put (PA and ABS) together in the right way,” says Waldschmidt.
Target automotive interior applications include instrument panels, center fascias, air and defroster vents and door assemblies.
Technyl Alloy already has one application deal — a center fascia on GM Daewoo Auto & Technology Ltd.'s new 5-door Kalos compact car. Rhodia soon will begin pitching the material to North American and European customers.
“That's the step we're about to take,” says Waldschmidt. “Some of our early focus will be at the OEMs and some of the Tier 1 suppliers who are interior systems suppliers. We feel it's a good opportunity for us to position a new product. It's a good area for us to participate in, in terms of growing our business.”
Interest from North American and European customers is key. Those markets account for 80% of Rhodia's PA applications, which in turn comprised 20% of the supplier's $8.3 billion in worldwide sales in 2001.
ABS has been mass-produced since the 1960s. The inexpensive thermoplastic is tough, hard and rigid, with good chemical resistance and dimensional stability. But it has a tendency to stress-crack.
Technyl Alloy offers better performance characteristics, including higher stress-cracking and heat resistance (up to 392°F [200°C]) as well as greater design flexibility — so the materials can be flowed into thinner sections, Rhodia says.
Because of Technyl Alloy's high fluidity, lower injection force and temperatures can be used, which reduces tooling and processing costs. Acoustics are improved, too, along with scratch resistance, Waldschmidt notes.
The resins also meet demands by auto makers for soft-touch and low-gloss interior surfaces, according to Rhodia. Technyl Alloy resins are lighter than competitive materials, too.
Early applications will be blow-molded. “But we'll be addressing injection-molded applications as well. That's something we'll be looking at in the future,” Waldschmidt says.
Rhodia's Engineering Plastics operations can produce Technyl Alloy at any one of eight plants. The company recently replaced its existing South Korean facility with a new $16 million plant with 20% more polyamide capacity. Rhodia also is considering expanding its Mississauga, Ont., Canada, facility.
Read more about:
2003About the Author
You May Also Like