Reducing Seat Mass a Science
Seating engineers have turned to the science of metallurgy in efforts to reduce seat-frame weight, employing many different metals and forging and casting techniques.
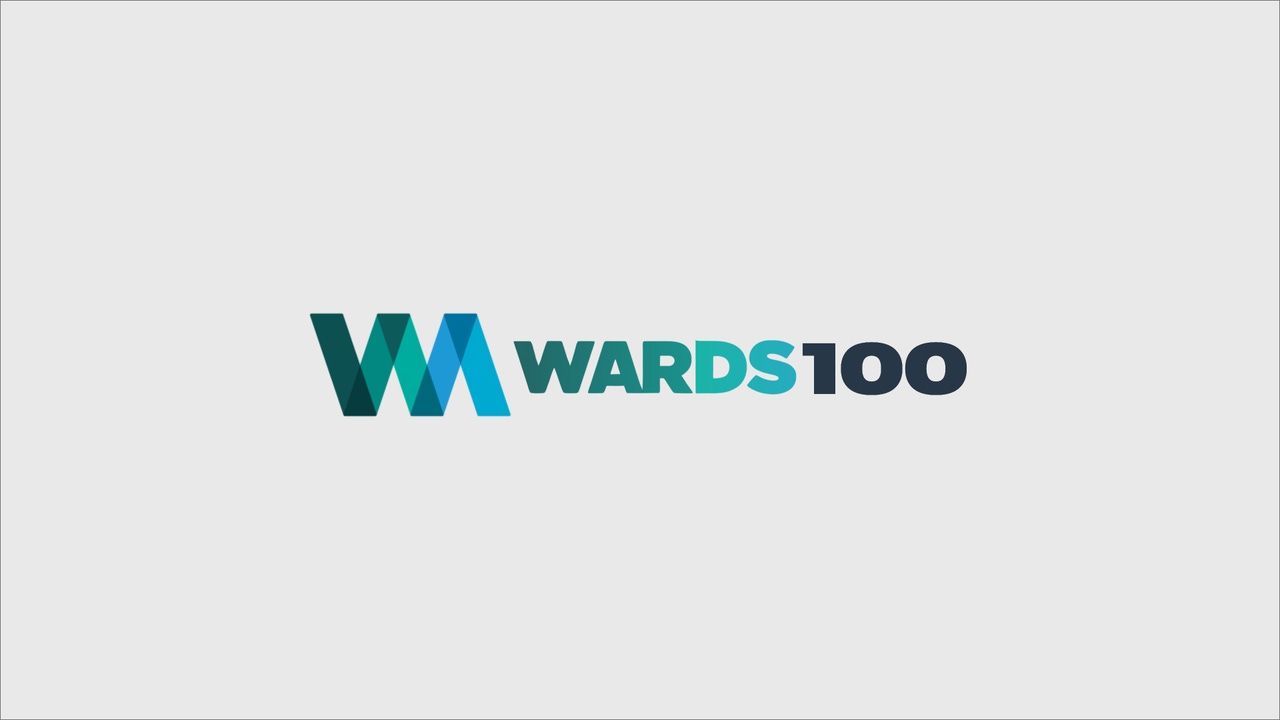
Special Coverage
Ward’s Auto Interiors Show

DETROIT – Rising fuel prices and looming stringent corporate average fuel economy regulations have auto makers and suppliers scrambling to take weight out of the vehicle, and reducing seat mass is a logical place to start, say two of the industry’s top seating experts.
In the not-so-distant past, automotive seats were relatively simple devices. But today’s seats are chocked full of sophisticated – and heavy – components, including heaters, motorized adjusters and lumbar support bars, says Jeff Corkins, chief engineer-research and development and new business development for Intier Automotive Inc.
Speaking at last week’s Ward’s Auto Interiors Show here, Corkins says seat frames present the greatest opportunity to reduce mass.
“If you want to take mass out of the seat, the big thing to attack is the frame structure itself,” he says. “There’s incremental opportunities in other areas, but you don’t get as much bang for your buck as putting your work into the frames.”
Seating engineers have turned to the science of metallurgy in efforts to reduce seat-frame weight, employing many different metals and a variety of forging and casting techniques.
High-strength steel is a popular choice among seat designers, but the material is difficult to form, process and weld, Corkins says.
In some cases, lower-strength steel is actually a better option, he adds.
“Some of these lower-strength steels are very formable, so you can stamp them and make shapes and bends and so on,” Corkins says.
Corvette Convertible top uses molded magnesium components.
However, HSS offers a cost advantage, because less of the material is needed in constructing the seat frame.
Either way, steel always will have a place in seat design, Corkins says, noting, “We know steel.”
Aluminum also is a popular choice for weight-conscious seat designers.
“In (the Chrysler) Pacifica, we actually have three rows of aluminum-backed frames,” Corkins says. “And in comparison to steel, the (aluminum) frames offer a 30% weight reduction.”
He says Chrysler LLC’s Stow 'n Go seats also have aluminum seatbacks.
“The drawbacks are you still have to put all the steel parts on, such as headrest guides, bolster wires and child-seat tethers, and you have to fasten them (with steel),” Corkins says. “So you get mass reduction, but there are trade-offs.”
Die-cast magnesium also is an emerging metal in the seat field. But die-casting requires the magnesium to be super-heated to 1,238° F (670° C), making it difficult to form intricate details.
“Like every other casting, there are areas that need to be (dimensionally) precise and need to be machined, and features such as holes need to be milled,” Corkins says.
The added time and expense of machining and milling die-cast magnesium has been a necessary evil. But a new method developed by Tier 1 supplier Magna International Inc., which owns Intier, may have solved the problem.
Ben Reginella, engineering manager for G-Mag International Inc., another Magna company, says molded magnesium represents the future of automotive seating.
“Magna spent quite amount of time developing a molded magnesium process,” he says. “It’s similar to plastic injection molding.”
Unlike die-casting, the molded magnesium process requires much less heat. And because the metal remains in a semi-solid state, it’s easier to form into precise shapes.
“We have a high degree of control because the solids are running at low temperatures,” Reginella says, adding the process also is closed-loop, so you don’t have the “die-casting haze” above the machine.
Additionally, little quality testing is needed on molded magnesium parts, also a result of the lower temperatures used during the process.
During the die-casting process, tiny bubbles can develop within the super-heated metal, compromising the strength and durability of the end product.
“That’s the reason (in die-casting) they have to do X-rays and checks,” Reginella says. “The outside skin will look completely fine, but what’s buried inside is what’s going to sneak up on you.”
The lower temperatures used in the molded magnesium process also lengthen the lifespan of steel tooling, produce higher-quality finishes and increase the weld-ability of the final part.
While the molded-magnesium process shows great promise, its use currently is limited to smaller components, Reginella says, noting that cell-phone manufacturers have been employing the process for years.
Currently, there are three magnesium-molded components on production cars – the mirror base on a number of Honda Motor Co. Ltd. vehicles, the liftgate housing for some General Motors Corp. trucks and portions of the top mechanism on convertible Chevrolet Corvettes.
“Right now the limitation is die size,” Reginella says. “(But) we’re aligned with Husky (Injection Molding Systems Ltd.) right now, and we’re building larger and larger machines.”
About the Author
You May Also Like