BMW Recruiting Engineers to Focus on Lightweight, Carbon-Fiber Composites
Carbon-fiber bodies long have been used for F1 race cars and supercars, but the German auto maker’s forthcoming i3 EV will be the first high-volume car to use the technology.
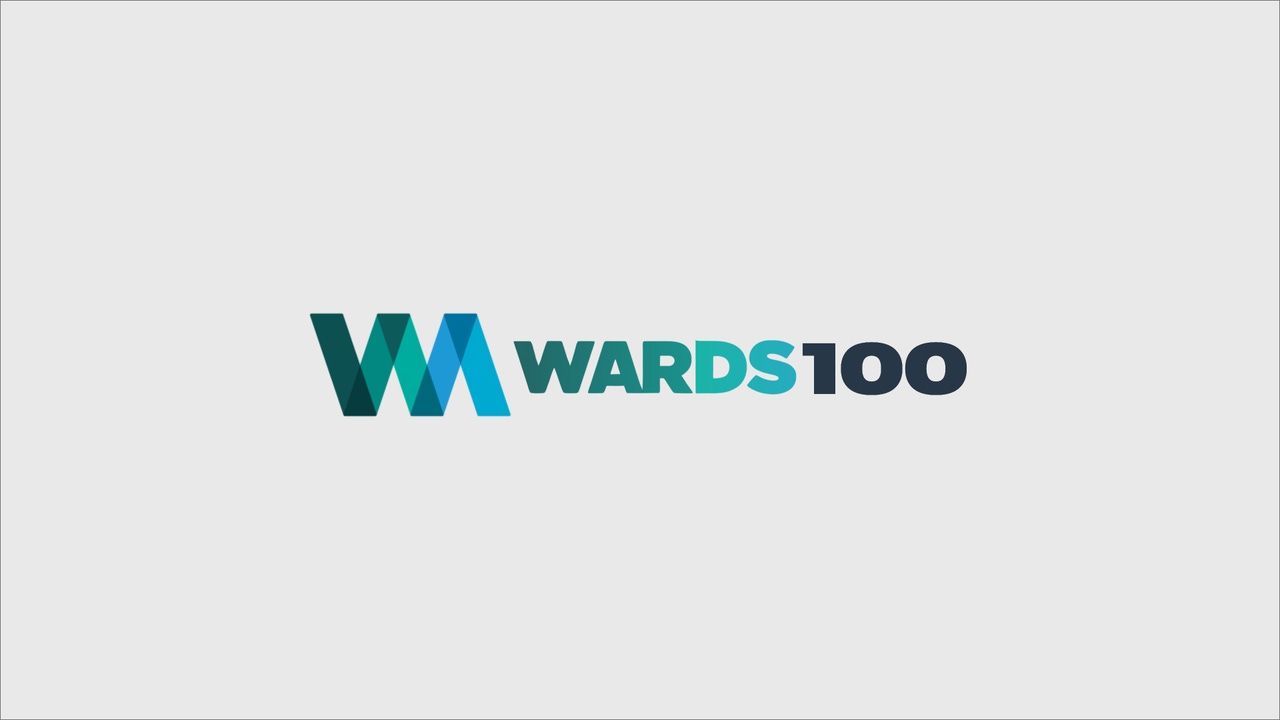
PARIS – BMW is recruiting 40 engineers with carbon-fiber expertise to help meet its goal of launching its i3 and i8 lightweight electrified vehicles in 2013.
BMW co-sponsored the JEC composite exposition here this year here to call attention to its job openings. Engineers and staff from the auto maker’s human resources department shared the BMW’s booth.
Carbon-fiber bodies long have been used for Formula 1 race cars and supercars, such as the Mercedes SLR McLaren Roadster, and carbon-fiber components such as roofs and spoilers are not rare on sporty cars.
However, the i3 will be the first high-volume car using the technology, which is based on a material costing as much as E20/kg ($13/lb.). BMW’s one-shift capacity is about 12,000 units annually for the electric i3.
The push to reduce carbon-dioxide emissions is behind BMW’s strategy.
“People are seeing that something has to change, and there are people who are willing to change their behavior,” says Hanno Pfitzer, a BMW process development engineer for CF bodies. “In 2050, 70% of the world’s population will live in cities. People need mobility, but they want to do it in a sustainable way.”
BMW launched its Project i in 2007, but it began building experience with carbon fiber in 2003 for series production of individual parts, such as the roof panel on the M3.
Now it will expand on that knowledge with the launch of the compact i3 EVC, previously referred to as the Megacity Vehicle, and the larger i8 plug-in hybrid, based on the Vision Efficient Dynamics supercar introduced at the 2009 Frankfurt auto show.
BMWi3 at JEC show in Paris. Tape conceals joints to prevent competitors from learning about vehicle’s adhesive strategy.
When BMW made an electric Mini E variant based on the Mini Cooper S, Pfitzer says it added 221 lbs. (100 kg) to the weight of the vehicle.
For an electric city car, BMW decided to compensate for the extra mass of a battery by reducing the weight of the car body, “and there is no lighter material than carbon fiber,” Pfitzer says. With lighter weight, the i3 will share the handling characteristics that are part of the brand’s heritage.
BMW’s design strategy harkens back to earlier days of car making, with a body-on-frame design. The powertrain will be part of an aluminum chassis that BMW calls its Drive Module, and the Live Module body will be a carbon-fiber structure resting on it.
The i3’s carbon fiber body-in-black is structural, made from preformed fabric pieces impregnated with resin injected in the resin-molding transfer method. Painted thermoplastic panels will be the visible skin of the car, but the roof will be a black carbon-fiber panel with a visible pattern, textile engineer Franz Maidl says.
The side panel on display in Paris has no B-pillar, suggesting the four sedan-style doors will incorporate the B-pillar function, similar to the Ford B-Max introduced at Geneva this year.
BMW has formed a joint venture with German carbon-fiber producer SGL Group. Its subsidiary, SGL-Automotive Carbon Fiber, in Moss Lake, WA, will produce the fibers, the rovings made with 50,000 fibers and the unwoven cloth used to make parts.
The U.S. plant begins production in the third quarter. BMW will make the body parts, itself , with tools and processes it has designed.
Having the JV and controlling the process from beginning to end is essential to the success of the program, Pfitzer says.
“The impregnation of the fibers by the resin is a highly complex process full of conflicting requirements,” he says in a written presentation. “On the one hand, the resin must reach every area of the material with minimal delay, impregnating every fiber right down to microscopic level.
“(But) as soon as it has impregnated all the material, the resin needs to harden as quickly as possible. Thirdly, a release agent is required that will allow the resinated components to be parted from the molding tools without the components being damaged. Resolving all these conflicting requirements simultaneously is a highly complex task.”
At the JEC event here, BMW says it is recruiting staff for conception and design of car bodies and undercarriages, process planning and process engineering, prototype construction, complete vehicle design and seat design.
Seat design likely is related to BMW’s effort to develop ways to recycle the large amounts of scrap in the carbon-fiber process. Pfitzer says an in-house process to recycle carbon-fiber waste is “in the final stages.”
About the Author
You May Also Like