Mother of All Processes
A decade ago, engineers still were talking about using computer-aided design and computer-aided manufacturing (CAD/CAM) simply to replace old-fashioned blueprints. Now its successor, product lifecycle management (PLM) software, is driving the entire vehicle development process. Without PLM, you would not have the number of launches or proliferation of models today, says Richard Gerth, a research scientist
August 1, 2006
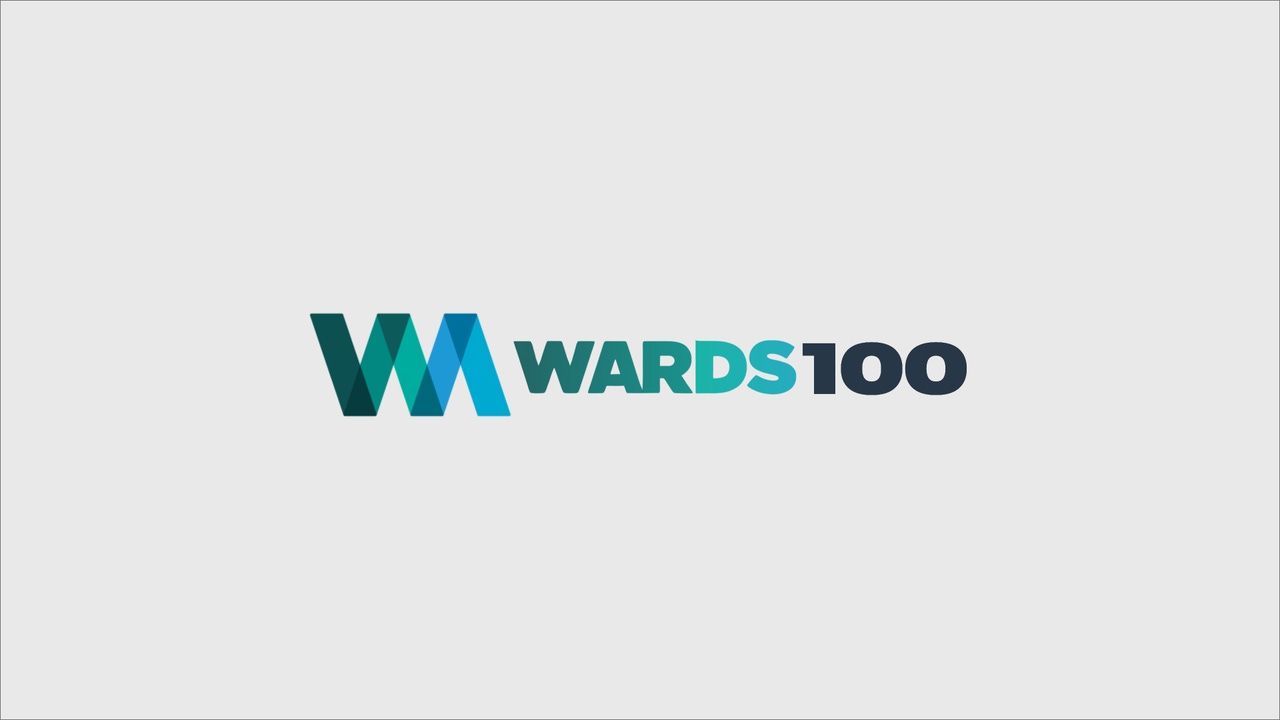
A decade ago, engineers still were talking about using computer-aided design and computer-aided manufacturing (CAD/CAM) simply to replace old-fashioned blueprints. Now its successor, product lifecycle management (PLM) software, is driving the entire vehicle development process.
“Without PLM, you would not have the number of launches or proliferation of models today,” says Richard Gerth, a research scientist with the Center for Automotive Research in Ann Arbor, MI.
“PLM is not CAD; it's not CAM; it's not analysis; it's not resource planning and it's not product-data management,” says Paul Zang, professor of mechanical engineering at Kettering University in Flint, MI. “PLM ties all processes together into a kind of mother of all processes.”
This now indispensable engineering software has a significant impact on revenue, quality, development speed and profitability. It manages the creation and distribution of design and engineering data globally, enabling designers and engineers to virtually see what parts, vehicles — and the plants that build them — will look like before any tooling is ordered.
Vehicles are more complex today than in previous eras, another reason PLM is so essential. “There are over 100 ECUs (electronic control units) in some cars today,” Gerth says. “That's going to increase.”
Software embedded in the chips manages myriad automated functions controlled by ECUs. “You have to manage all the ECU relationships,” says Eric Sterling, vice president of UGS' North American automotive business. “You can't do that with people anymore,” he says. The solution is PLM.
And as more complex platforms, such as those for hybrid-electric vehicles and fuel-cell vehicles, go into production, PLM is the essential strategy to control the huge amount of data used to run the advanced electronics. Ultimately, it will have a significant impact on revenue and profitability as new generations of vehicles are developed.
UGS Corp. of Plano, TX, and Paris-based Dassault Systemes are battling for leadership of the automotive PLM market that totals more than $3.2 billion annually.
The automotive PLM sector has evolved from the best software used by a range of industries: aerospace to apparel makers. Its use by OEMs and suppliers now is growing exponentially. There were only about 1 million lines of code in vehicles during the 1990s, says Kevin Reale, an analyst with AMR Research in Boston. “This could grow to more than 100 million lines of code in five to eight years,” he says.
Part of this is due to mushrooming mechatronics systems. OEMs and suppliers are also pressured to design vehicles and components faster and get the products right the first time. Failure to design in quality is expensive. Ford Motor Co. spent almost $4 billion in warranty costs last year — about 3% of its 2005 revenue, says Reale, based on U.S. Securities and Exchange Commission data. Overall industry warranty claims reached $13 billion in 2005.
Reale says 52% of the recalls resulted from electronic, fuel, brake or speed-control failures. Almost three-quarters of recalled parts were electronically controlled — and about 35% had embedded software.
With PLM, auto company designers, engineers and manufacturing experts can share knowledge quickly and attack quality and durability issues globally. “PLM increases the reliability of communications,” says CAR's Gerth. “It's important to prevent delivery of wrong data. That's not possible without PLM,” he says.
About 70% of vehicles that premiered at the North American International Auto Show in Detroit last January were developed with Dassault's CATIA software used for CAD/CAM. CATIA now is purchased by auto makers in Asia, Europe and in the U.S. The major company Dassault doesn't supply is General Motors Corp.
UGS, once part of EDS (formerly owned by GM) is GM's exclusive PLM provider. UGS PLM software also is used by BMW AG, Ford and its Premier Automotive Group brands, Nissan Motor Co. Ltd., Suzuki Motor Corp. and suppliers such as Delphi Corp. and Hella KGaA Hueck & Co.
Nissan is in the midst of a program to develop 28 new models. It claims to have cut product development cycle time to as little as 10.5 months with UGS' NX CAD software.
Kirk Gutman, GM's chief global information officer for manufacturing and quality control, says digital-assisted software for manufacturing “was not very useful until three years ago.” The software and hardware now have hit a price point that's cost effective, he continues. “The software is also finally scalable to the order of complexity that it takes to do a (vehicle assembly) plant.”
GM now stores all data, ranging from an entire plant to each individual robot. “At GM, we use PLM for every new line in the Lansing (MI) Delta Township plant and its sister factories in China and Poland,” he says. “It gives us full collaboration across the globe.”
Gutman says the international divisions now share information on central manufacturing, virtual-assessment centers, and product and design reviews globally.
For instance, when a plant needs a new conveyor for a robotic door line, manufacturing engineers can pull it out of software libraries. “It can be replicated across the globe,” he says. GM engineers also optimize stamping press throughput with simulation software. Its product engineers even share information on the integration of weld points.
“We write a lot of the algorithms in-house, but we also do a lot of it with UGS,” Gutman says. “The biggest return in doing things digitally is the ability to get things right the first time.”
Digital engineering also makes it easier to reuse previously designed parts. The software makes it quicker to find parts that are placed around or touch each other. Of course, there's a downside to parts reuse: If the part has failures in one model, it can spread to every other model that uses the component.
Gutman says PLM is especially useful for finding interference problems in plant design. “If a pipe in a factory would run through another pipe, virtual manufacturing makes it easier to spot and fix.”
He says GM achieves a 20% saving on rework and an overall time reduction of 20% by eliminating interference with PLM.
“GM saves more than $1 billion annually with UGS PLM,” Sterling says.
UGS' Teamcenter coordinates all other software used to design, engineer and assemble vehicles. It even helps auto makers track products after they're sold — all the way to the crusher — by easing compliance requirements and disposal of hazardous materials.
Additionally, Teamcenter allows engineers to virtually build a vehicle by mapping out the entire development process and produce 3D parts and models before tooling is purchased. This has cut GM's development time for some models to as little as 24 months.
UGS PLM also can predict the performance and durability of parts while they still only exist in cyberspace. The software can simulate the stamping process and how it affects the behavior of stamped metal. Afterwards, the system even designs dies.
Teamcenter is used to simulate vehicle crashes and predict stress and strains on parts. However, the auto industry lags far behind airplane manufacturers in using this capability. Planes are not crashed to determine their crashworthiness. It's all done through simulation, and government regulators review the data.
Keeping track of revisions also is easier with PLM, says John Heidern, a UGS executive. “The system is smart enough to say ‘this has been updated,’” he notes.
Ford used Teamcenter in 57 worldwide vehicle programs, enabling it to achieve “significant” cost savings, UGS says. But the company also sources Dassault's CATIA V5 software and used it to develop the Fusion midsize sedan. Ford engineers then quickly developed the Lincoln Zephyr and Mercury Milan with the same software.
UGS' Sterling says PLM makes designing parts easier. For instance, engineers can virtually design a hose and determine its routing to make sure water flows through the part the way it was designed. If the hose doesn't perform as expected, a solution can be created quickly online with UGS' Tecnomatix software before tooling is ordered.
PLM even shows engineers what impact a design change might have for manufacturing requirements. Digital manufacturing software can simulate high-speed transfer lines in a plant and aid manufacturing floor planning. UGS' Tecnomatix can track the flow of components to assembly stations and even check individual worker movements and what tools they will need at those points.
PLM also enables manufacturing engineers to determine what will happen to a vehicle when line speed is increased.
Read more about:
2006About the Author
You May Also Like