Old Process Offers New Possibilities
TOLEDO, OH - Bang! Everybody jumps. At least everybody standing near an unusual looking machine here at the engineering center of Dana Corp.'s Driveshaft Div. Jim Duggan, chief engineer of advanced design, apologizes for the commotion and says the actual production process is much quieter.But the noise seems appropriate because Mr. Duggan says the closest thing to what is being demonstrated is something
January 1, 1999
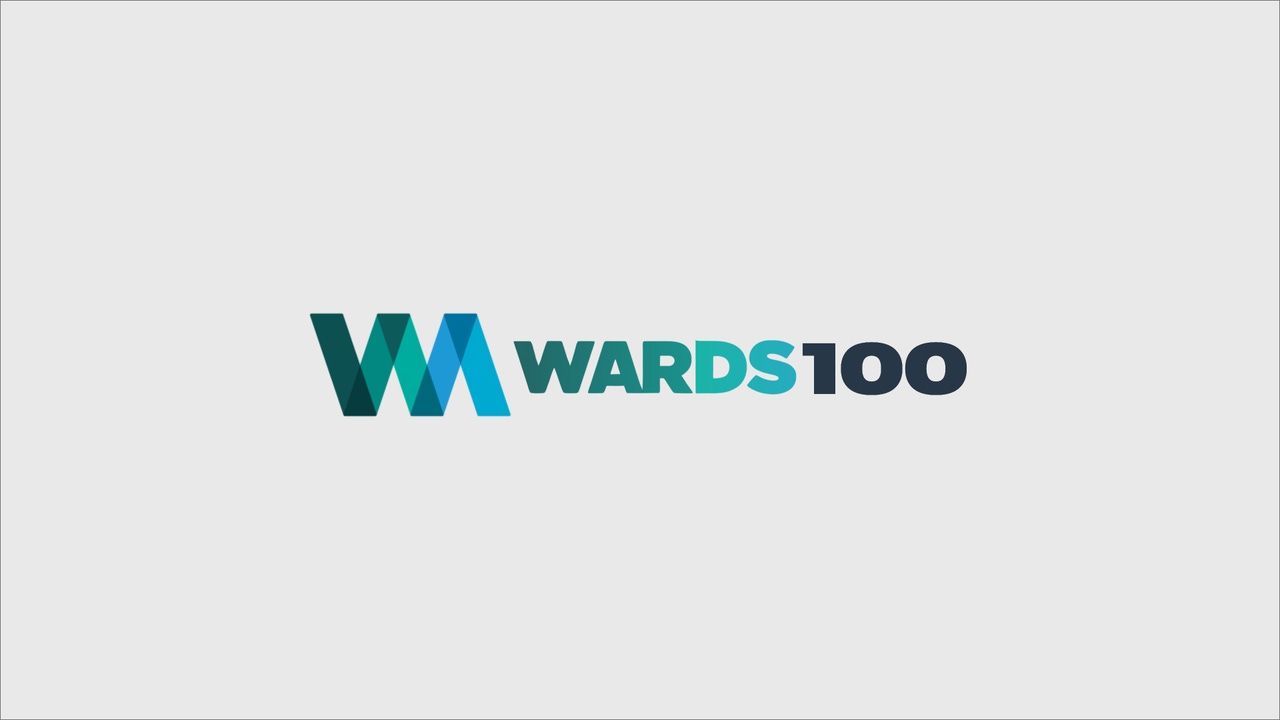
TOLEDO, OH - Bang! Everybody jumps. At least everybody standing near an unusual looking machine here at the engineering center of Dana Corp.'s Driveshaft Div. Jim Duggan, chief engineer of advanced design, apologizes for the commotion and says the actual production process is much quieter.
But the noise seems appropriate because Mr. Duggan says the closest thing to what is being demonstrated is something called "explosion welding."
What has happened: a specially designed electromagnet using over 1 million amps and 5,000 volts of electricity created an intense field of magnetic energy that tightly crimped the edge of an aluminum driveshaft tube in the blink of an eye.
In regular production, a round steel component would be inserted in the end of the tube, muffling the sound as the aluminum tube collapses inward so fast it forms a metallurgical bond with the steel.
The process, called magnetic pulse welding, makes a joint as strong as a conventional weld, but it produces almost no heat, uses much less energy and doesn't require shielding gases or welding wire. Most importantly, it provides the capability to weld dissimilar metals such as steel and aluminum - normally a nearly impossible task.
Variations of magnetic pulse welding and magnetic pulse forming have been used for 60 years, but mostly for connecting small-diameter tubes. Dana's innovation offers the ability to produce strong, uniform welds on much larger tubes such as driveshafts.
Dana is developing this welding method because it will allow the giant auto supplier to make lighter, more compact driveshafts for cars and light trucks. But it has many other potential uses. Dana sources say it also could be used to build lightweight vehicle space frames that combine aluminum and magnesium structural members with steel parts such as corner nodes for an overall structure that is both lightweight and low-cost.
Every material has certain strengths and weaknesses, Mr. Duggan explains. "Steel components can withstand the high stresses associated with small-diameter splines, and aluminum provides the advantages of light weight and corrosion resistance," he says. Magnetic pulse welding allows Dana to convert most of the driveshaft to lightweight aluminum while keeping certain high-load parts in steel. It also provides the ability to manufacture more innovative multi-piece driveshafts.
Equipment capable of volume production is expected to be ready this year, and steel/aluminum hybrid driveshafts made with magnetic pulse welding should be on production vehicles within the next five years, Mr. Duggan says. - Drew Winter
You May Also Like