SKF Introduces Fuel-Saving Bearings
Many Fuel-Economy Improvements come from downsizing engines and chopping weight, but reducing friction in a vehicle's multitude of moving parts promises to play an important role in improving the efficiency of future vehicles. Based on this assumption, Sweden-based SKF Group is introducing a new line of energy-efficient bearings for powertrain applications, including tapered roller bearings, driveline
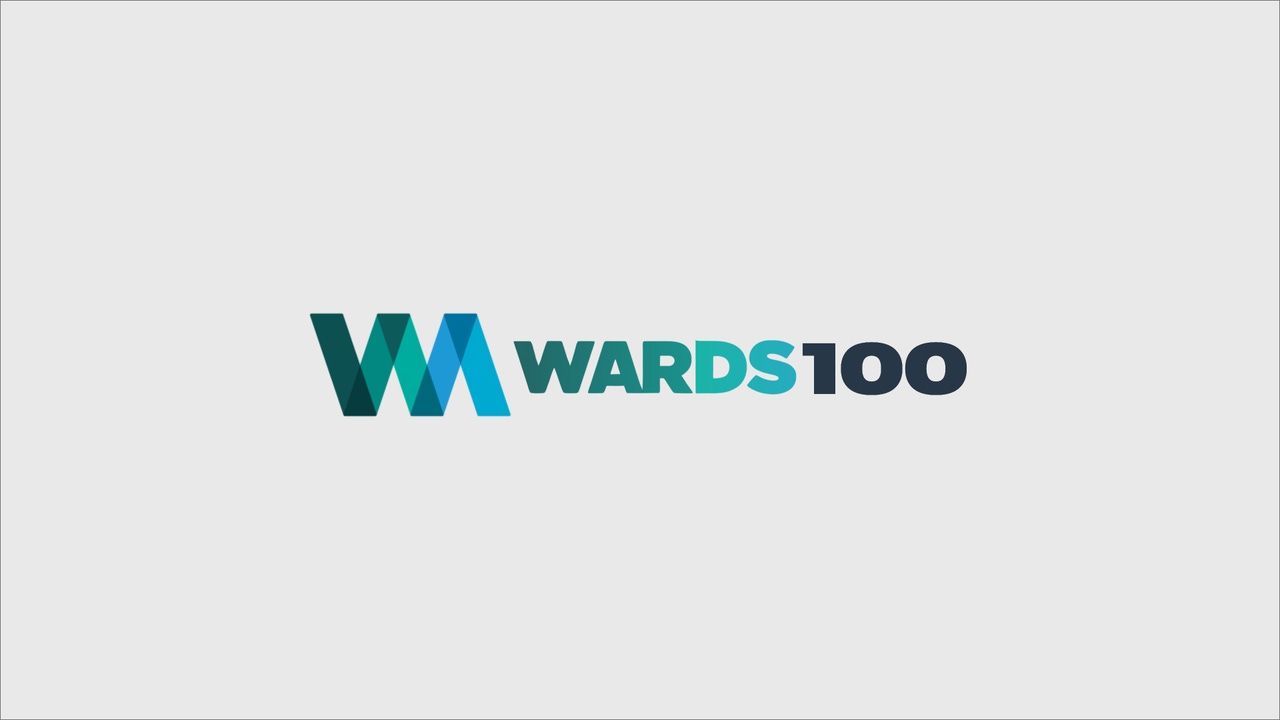
Many Fuel-Economy Improvements come from downsizing engines and chopping weight, but reducing friction in a vehicle's multitude of moving parts promises to play an important role in improving the efficiency of future vehicles.
Based on this assumption, Sweden-based SKF Group is introducing a new line of energy-efficient bearings for powertrain applications, including tapered roller bearings, driveline angular contact ball bearings and “hybrid” bearing units that combine the strength of both ball- and tapered-roller bearings for specific applications.
The supplier estimates the new bearings can reduce friction up to 30% and as a result curtail carbon-dioxide emissions by up to 13 grams per mile for an all-wheel-drive powertrain.
However, achieving such dramatic results requires complex computer simulation and modeling to optimize internal bearing geometry enough to significantly lower resistance to vehicle acceleration and engine torque, says Thomas Wolf, senior application engineer at SKF's Car Business Unit in Schweinfurt, Germany.
To do this, SKF has developed a software program called the Vehicle Environmental Performance Simulator that enables engineers to analyze loading conditions on any bearing and the corresponding impact on bearing friction torque and power loss for a given load cycle and car model.
That means SKF engineers can determine torque levels based on specific load cycles, which in turn makes it possible to calculate, via the gear-wheel's geometry, the corresponding bearing loads on rollers or balls that are responsible for the most friction.
By knowing specific load levels, the resulting stress levels and other factors, such as stiffness and bearing life, engineers can optimize the bearing's internal design features, including contact angles and raceway profiles, to reduce friction. The bearing raceway's roughness and topography also can be optimized for proper oil-film buildup.
When bearing power losses have been determined, it is possible to estimate, based on engine type and configuration, the fuel consumption and related CO2 emissions, Wolf tells Ward's at a recent event in Detroit.
In today's powertrains, tapered roller bearings generally are used to support shafts because they are best in applications with high specific load levels, while ball bearings generally provide the highest benefit in applications with low and moderate loading.
To take advantage of the benefits of both types of bearings, SKF has added new types of energy-efficient bearings to its product range that give auto maker engineers more latitude in choosing which bearing type is best for a given situation, as well as “hybrid” bearing units that can offer the best of both worlds.
The decision as to which bearing type is best suited for a particular application must be considered as a whole and take into account bearing functions such as stiffness and service life, Wolf says.
So far, several premium German auto makers and some key gearbox suppliers have been receptive and are starting to implement the new concepts, Wolf says.
SKF says auto maker and Tier 1 engineers also can use SKF's VEP software tool to explore the merits of the various design options.
Demand Explodes for Fuel-Saving Technology
subscribers.WardsAuto.com/ar/demand_explodes_fuel_090625/
Road to 35 MPG Uphill Climb
subscribers.WardsAuto.com/ar/road_35mpg_uphill_090421/
GM Reveals Secrets of '09 Cadillac CTS-V
subscribers.WardsAuto.com/ar/gm_speed_secrets/
Read more about:
2009About the Author
You May Also Like