Versatility, NVH Hallmarks of Pentastar
Outside of Chrysler and its dealerships, few knew the auto maker's Dodge, Ram, Jeep and Chrysler-brand vehicles were powered by seven different V-6 engines. Soon, there will be just one: the 3.6L DOHC Pentastar V-6. And, because it's a Ward's 10 Best Engines award winner in its debut year, that bodes well for the auto maker's burgeoning new lineup of cars and trucks. The engine program, internally
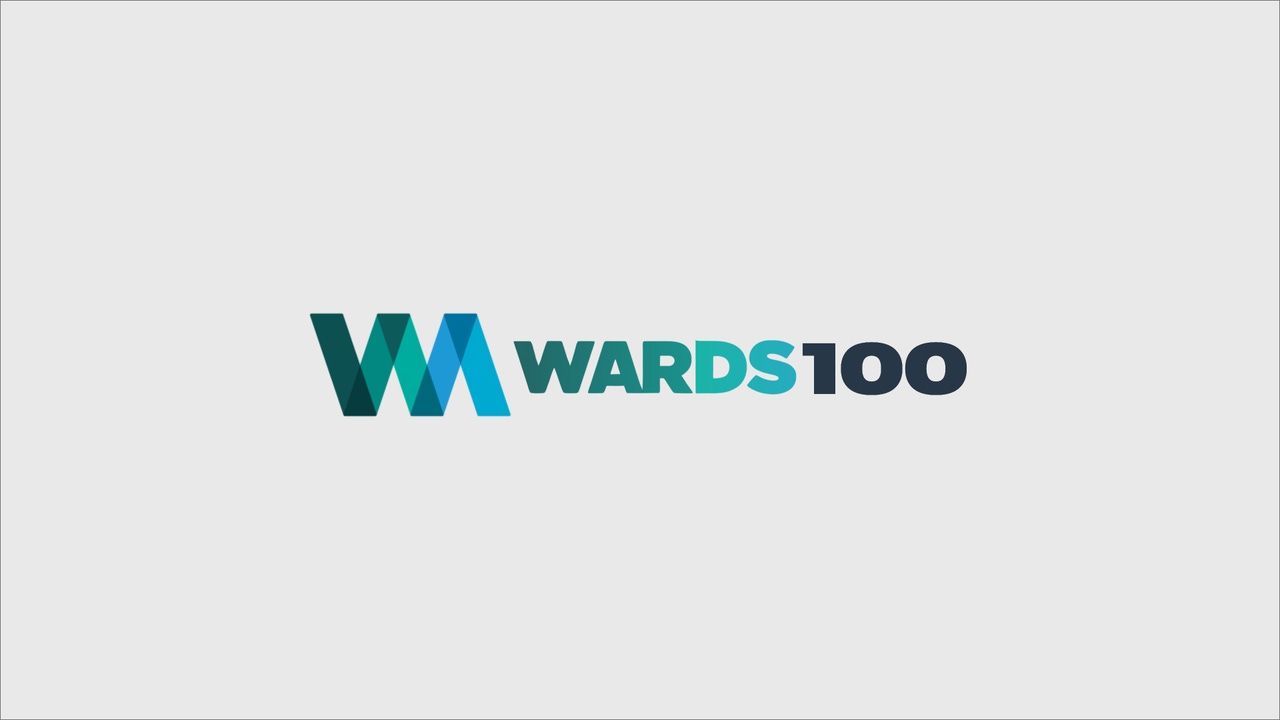
Outside of Chrysler and its dealerships, few knew the auto maker's Dodge, Ram, Jeep and Chrysler-brand vehicles were powered by seven different V-6 engines.
Soon, there will be just one: the 3.6L DOHC Pentastar V-6. And, because it's a Ward's 10 Best Engines award winner in its debut year, that bodes well for the auto maker's burgeoning new lineup of cars and trucks.
The engine program, internally known as Phoenix, dates back to the late 1990s, before Daimler took over the company.
Then, following the “merger” that created DaimlerChrysler, there was an attempt to do “some level of commonization on an engine that could be used for both companies,” says Pentastar program chief engineer Chris Cowland. Two separate teams worked on it for a while on both sides of the Atlantic.
But there were fundamental differences in needs: Daimler wanted a 90-degree V-6, while Chrysler insisted on a more compact 60-degree V-6 for packaging and balance.
Daimler's engine would mount north-south in rear-wheel-drive vehicles; Chrysler versions needed to be designed so they also could be placed east-west (transversely) in front-wheel-drive vehicles.
So the two efforts diverged. And when Daimler later sold Chrysler, it became a Chrysler-only project again, first under Cerberus ownership and then under Fiat.
One major challenge was the need for incredible versatility. “Imagine trying to configure an engine that can fit into 13 different models with the fewest possible changes. That was one of the design briefs,” Cowland says.
“Packaging an engine is tough enough, but when you have 13 different vehicles — in some it's going across, in others it's lengthwise — that was a big one.”
Another challenge was keeping internal modifications to a bare minimum. “To get the economies of scale we needed, it was critical to avoid proliferation of components,” Cowland says.
There are no internal component changes between current applications, just slight external differences. The inlet manifold is on a different side for north-south vs. east-west applications, and there are two front accessory-drive layouts, one with the alternator on the right side and one with it on the left. But the pistons, crankshafts, cylinder heads, even the camshafts are all identical, Cowland says.
Still, applications are calibrated differently. The Pentastar in the Dodge Challenger, with the lowest induction restriction and exhaust back pressure, pumps out a hefty 305 hp and 268 lb.-ft. (364 Nm) of torque.
In the Grand Cherokee, with different conditions, the engine generates 290 hp and 260 lb.-ft. (353 Nm). Turned around in front-drive applications (including our test Dodge Avenger), the restrictions are higher, partly because the front bank's exhaust runs under the engine, and the output is lower at 283 hp and 260 lb.-ft. (353 Nm).
The dual independent cam phasing strategies also are different on some engines.
“Rear-drive applications allow us to scavenge quite efficiently because of the way the exhaust is configured,” Cowland says. “But we have a different phasing strategy on front-drive applications because scavenging is more difficult.”
Design objectives that focused on five customer attributes — performance, efficiency, environmental impact, cost of ownership and refinement — drove hundreds of engineering goals on the Phoenix program.
To achieve targeted levels of refinement, for example, the team selected engines that were best-in-class in key noise, vibration and harshness areas such as radiation noise, induction noise, mount vibration and torsional excitation.
Metrics for refinement then were developed in each area based on the benchmark engines.
“We identified the best engine in class for each of those metrics. Our target was to equal or beat that very best engine in each area,” Cowland says. “That is no easy feat.”
Chrysler engineers also wanted zero brackets on the engine. “Brackets cost money,” Cowland says.
“To get this high level of refinement and noise performance, it was important to have very high natural frequencies of vibrations for auxiliary mountings. So (accessories) all bolt directly to the structure of the engine, which is pretty unusual, and it was a big challenge to come up with an accessory drive layout that works in all applications, both front- and rear-wheel drive.”
Other challenges came with new technologies, including a variable oil pump system that runs in low mode to deliver about 36 psi (2.5 bar) of gallery oil pressure below 3,000 rpm, then shifts to high mode to generate just over 58 psi (4 bar) at higher engine speeds.
Another is a totally integrated exhaust manifold. All of the exhaust manifold geometry is contained within the aluminum cylinder head, and the close-coupled catalyst bolts directly to it.
“Imagine taking a traditional exhaust manifold and creating all of its flow paths inside the cylinder head within the water jacket,” Cowland says.
“The ports from each cylinder's two exhaust valves flow together, and then a bend joins those three pairs of ports into a single, roughly oblong exit out of the side of the head into the catalyst. And our flow paths are as good as they would be with a typical external manifold, and smoother.”
Because this strategy created some daunting thermal loading conditions, the team used advanced computational fluid dynamics and thermo-mechanical fatigue analysis to simulate, analyze and design to handle any that occur.
“This is not bookshelf technology,” Cowland say. “We were developing something relatively new and brand-new for Chrysler.”
Is there room for improvement as customer, competitive and corporate average fuel economy demands ramp up relentlessly over the next several years?
Cowland confirms gasoline direct injection is being tested, and considered, but top Chrysler powertrain executives have voiced serious concerns about GDI as a long-term strategy because of cost, noise and other issues.
Fiat's MultiAir-valve control technology also is being looked at for the Pentastar. “We've de-throttled the engine a lot with our cam-phasing strategy, so some of the benefits of MultiAir have already been taken,” Cowland says.
“But we're looking at how we could fully utilize the capability of MultiAir to make the engine even more efficient.”
Also, it's no secret Chrysler has two new automatic transmissions coming soon, an 8-speed for RWD applications and a 9-speed for FWD — that will team with the Pentastar V-6 to make the vehicles it powers more efficient.
“Those transmissions will enable us to operate the engine under different drive cycles in real-world conditions so we can re-optimize our combustion, scavenging and valve-timing strategies,” Cowland says.
This highly refined and versatile new Pentastar V-6 will power 10 Chrysler vehicles by the end of this year and 13 by 2013.
By then, it will have replaced all seven older V-6s and likely will account for more than a third of the company's powertrains. It also is projected to improve Chrysler's overall CAFE 25%.
Did the relatively brief partnership with the Daimler team make this engine better than it might otherwise have been?
Insiders say the relationship with the German auto maker was strained and created a tedious and time-consuming decision-making process, but Cowland is diplomatic.
“I think collaboration brings different viewpoints to a program,” he says.
“Companies have different fundamental design philosophies, and there always is some positive that comes out of being able to interface with engineers with slightly different perspectives.
“There were things that Chrysler learned from working with Daimler, and I know that Daimler learned some things from Chrysler.”
— with Drew Winter
ENGINE SPECS
CHRYSLER GROUP LLC
3.6L DOHC PENTASTAR 60° V-6
Displacement (cc): 3,605
Block/head material: aluminum/aluminum
Bore × stroke (mm): 96 × 83
Horsepower (SAE net): 283 @ 6,350 rpm
Torque: 260 lb.-ft. (353 Nm) @ 4,400 rpm
Specific output: 79 hp/L
Compression ratio: 10.2:1
Assembly site: Trenton, MI; Saltillo, Mexico
Application tested: '11 Dodge Avenger
EPA city/highway (mpg): 19/29
The Ward's 10 Best Engines competition has recognized outstanding powertrain development for 17 years. In the second installment of the 2011 series, Ward's looks at the development of Chrysler's new V-6.
WARDSAUTO.COM
Chrysler Group LLC: 3.6L Pentastar DOHC V-6 subscribers.wardsauto.com/ar/chrysler_group_pentastar_101216/
About the Author
You May Also Like