Shrinking Time - Can Japanese bring a car to market in 18 months?
TOKYO - With last autumn's introduction of the Mazda Capella and Honda Accord, Japanese carmakers have again raised the bar for bringing new products to market.If pressed, most manufacturers can now develop a model in 36 months from initial concept to production. However, they prefer to work within a48-month time frame. The period is somewhat longer for luxury cars like the Niss an Cima/Q45 and Toyota
March 1, 1998
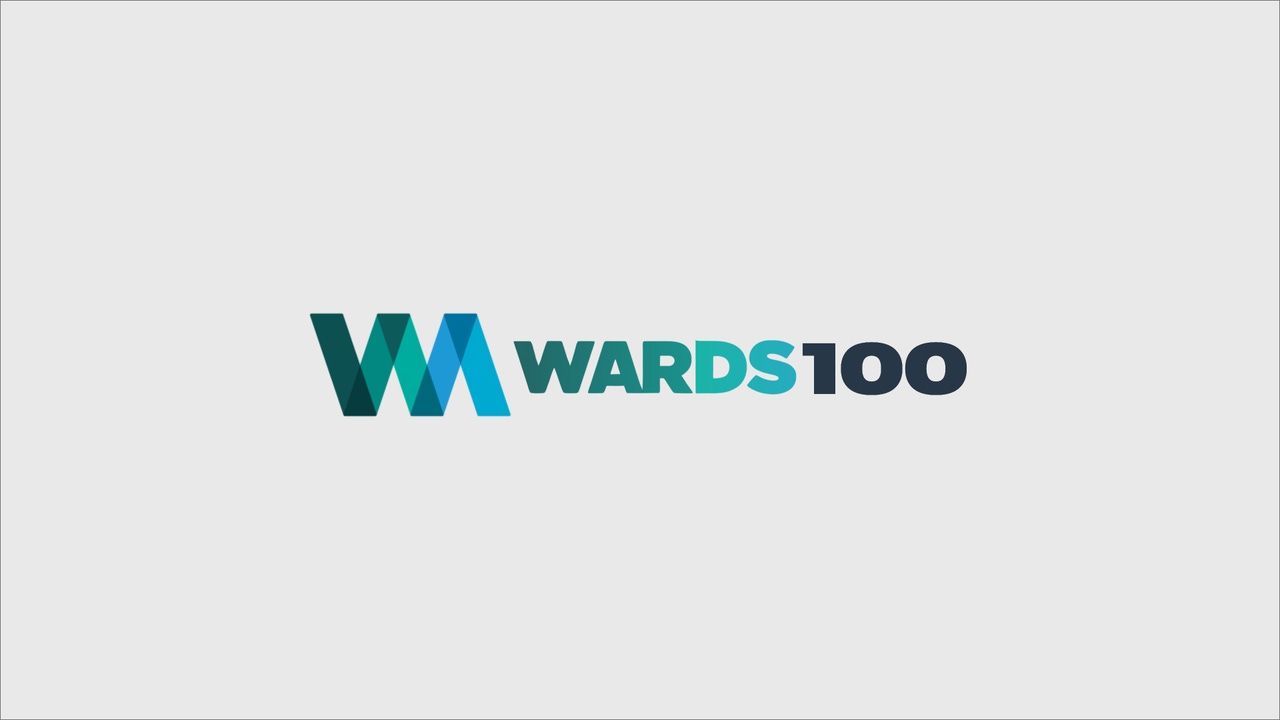
TOKYO - With last autumn's introduction of the Mazda Capella and Honda Accord, Japanese carmakers have again raised the bar for bringing new products to market.
If pressed, most manufacturers can now develop a model in 36 months from initial concept to production. However, they prefer to work within a48-month time frame. The period is somewhat longer for luxury cars like the Niss an Cima/Q45 and Toyota Celsior/LS400. Engine development is longer as well, ranging from 48 months to 60 months for conventional powerplants. This is again from initial concept. Alternative engines such as "hybrids" and gasoline direct injection units require more time.
For the most part, Japanese carmakers can engineer a model in 20 to 24 months, bringing it to production from so-called "design freeze." Their interim target is 18 months, which most expect to achieve by the year 2000. Longer-term, by the early 21st century, senior product planners feel that 12 to 15 months is feasible. Even now, 12 months is reachable for derivative models with high carry-over and with 60% to 90% shared components.
Despite the industry's desire to compress the development process, there is disagreement about the need to do so. Lance Ealey, an automotive analyst for McKinsey & Co. in Cleveland, argues that it's better to be "right" than to be "first."
"It's more important to have a strong concept," he says. "Take the Honda CR-V and Suzuki Wagon R, both incredibly successful in their respective segments. Although other models in those categories came to market earlier, the CR-V and Wagon R have exceeded most people's expectations because they started with robust concepts."
Mr. Ealey warns that in their haste to bring a new models to market companies must "guard against hurrying concept development." Otherwise, he says, "even if the engineering program is flawless, market reaction might be less than anticipated."
Still, the industry is likely to continue cutting development time. First, this allows companies to react more quickly to a competitor's product, which is especially important if that product is a hit; witness Honda's quick response to Toyota's RAV4 sport/utility. Second, costs are reduced, particularly labor costs, which constitute an estimated 30% to 40% of the total development budget, excluding tooling.
Of recent models, Mazda brought the Demio to market in just 15 months and the new Capella in 19 months. Toyota's Ipsum minivan took 151/2 months (four years from initial concept). At Mitsubishi, the Pajero Mini, incorporating 60% of common parts, was ready in just 20 months; the Chariot minivan was launched in 19 months. Nissan is slightly slower, though not by much. The Primera and Renessa wagons, both unveiled last autumn, took 20 months and 22 months, respectively. In fact, all car companies in Japan claim to have cut engineering time in half since the beginning of the decade.
SLASHING COSTS...
Hand in hand with speeding process time, development costs have been slashed to levels unheard of five years ago. The current investment required to develop a base C and CD-class model such as the Toyota Corolla and Camry, Honda Civic and Accord or Mazda Capella is estimated at $200 million to $250 million (using a $1/125 Yen exchange). The sum includes new tooling for a single plant. It does not include supplier costs, which generally are passed onto the carmaker through the life of the model. Japanese car companies still outsource 60% to 70% of componentry by value.
The figure also does not include derivative models for sale in single-country markets and multiple body types. For instance, cars like the Honda Domani (a domestic derivative of the Civic) and Mazda Demio (a derivative of the Revue/121) would cost between $50 million and $75 million if they were developed today. Likewise, a hatchback or wagon, built off a base sedan and sharing a lot of componentry, could cost around $50 million. Honda estimates that the total development budget for the new Accord (for all five models, including a Japanese wagon and sedan, North American sedan and coupe, and European sedan) was between $500 million and $550 million, including tooling at three plants inside and outside of Japan.
Costs will vary depending on the need to adopt advanced engine control and safety systems. U.S. and European models, which are equipped with dual-front air bags, antilock brakes and special reinforced bumpers, tend to be more costly to develop than models for Asia. In addition, development costs for upscale models like the Cima/Q45 or Celsior/LS400 are higher than for midsized and compact models, though only by an estimated 10% to 20%, unless the car is being introduced to the market for the first time. Then it would cost more. For instance, the original LS400, were it developed today with no shared components, would cost an estimated $350 to $400 million, still well below the car's mid-1980s budget.
Costs also vary depending on the number of new components. Mazda's new Capella sedan, for instance, has an estimated 30% shared or carry-over components. Five-door hatchback and wagon derivatives share 80% of componentry with the base model. Development cost of the base model including tooling was under $240 million. In contrast, the Demio, with 60% shared componentry, reportedly cost $72 million.
Standard engines generally cost $8 million to $16 million to develop. The combined cost for engine development including new tooling and machining is around $160 million. New engines such as Mitsubishi's GDI are estimated to cost two to three times more than conventional engines - somewhere between $24 million and $40 million.
REDUCING PLATFORMS...
One of the keys to bringing costs under control is reducing platform numbers, which ballooned during Japan's economic "bubble." Says Ken Hashimoto, a senior engineer at Honda's Tochigi R&D Center: "Optimizing platforms is a key to raising efficiency at our production sites. The more flexibility we achieve, the greater potential there is for savings."
Honda currently has six main platforms (seven including the low-volume NSX sports car). Although the company does not foresee a significant reduction, it intends to build multiple models off of each. For instance, borrowing from the basic Civic platform, Honda engineers already have developed the Domani, CR-V and Orthia.
Elsewhere, Toyota plans to reduce its platform total, excluding commercial vehicles, from around 15 to five or six by the early 21st century; Nissan's target is about five, from 24 today; and Mitsubishi's is five, from seven or eight.
Mazda, which previously had planned to reduce its total from five to three, is currently in a state of flux as the company is in the process of integrating many of its platforms with Ford. As things stand today, Mazda will take the lead engineering role for the future "B," "C" and "CD" segment products - namely the Revue (including the Ford Fiesta), Familia, Capella and Millenia. The company will also handle sport/utility derivatives of those models.
Insiders contend that the Familia and Capella, which are likely to serve as the base for the future Contour and Mystique, will be merged into a single platform.
MAKING PLATFORMS FLEXIBLE...
For most Japanese carmakers, like their counterparts in the United States and Europe, platforms are determined by a combination of powertrain (engine and transmission), driveline design (front-wheel, rear-wheel or 4-wheel drive), suspension, underbody dimensions and components, wheelbase, traction width, sheet metal, etc.
Through development of new techniques to stretch and widen platforms, the conventional definition of "platform" is changing. For a number of years Japanese carmakers have had the ability to lengthen or stretch platforms. Witness the Odyssey and Ipsum minivans, built respectively off the Honda Accord and Toyota Camry platforms. But with development of the new Accord last autumn, Honda succeeded in widening the platform.
Engineers accomplished this by moving the car's gas tank between the rear tires. That enabled them to introduce a series of special brackets to hook the wheels to the car's inner subframe. Adoption of these brackets - for which the automaker has applied for several patents - allows designers to push the wheels together or pull them apart, in effect narrowing or lengthening the car's wheelbase. More importantly, it enables the company to manufacture different sized models without major additional investment in body assembly equipment.
Honda, which began development of the "flexible" platform shortly before launching of the 1993 Accord, subsequently developed three sets of brackets - for Japan, North America (6.3 ins. [160 mm] longer and 3.5 ins. [90 mm] wider than the Japanese model) and Europe (similar length to the American model and similar width to the Japanese model). More importantly, off the same platform, the automaker has developed five models - the front-drive North American Accord sedan and coupe, a Japanese Accord sedan and wagon, both with 4WD capability, and a front-drive European Accord sedan scheduled for autumn introduction. The Accord that's being assembled in Thailand and other points in Asia essentially is the American model. All models, with the exception of the Asian Accord, feature different interior and exterior designs.
Naturally, more was involved than just stretching or widening the platform. For instance, Honda engineers had to make modifications in the suspension assembly. They did so by connecting the suspension arm to the subframe, then joining the subframe assembly to the body. In the previous generation Accord, only the front suspension was connected to the subframe.
Other Japanese carmakers are now following suit. Nissan's Sunny and Bluebird (produced and sold in North America as the Pulsar and Altima) reportedly will adopt a "flexible" platform, as will the revamped Toyota Corolla in 1999.
Once Toyota gets its platform number down to six, the company will employ an "evolving" strategy, according to Kazuo Okamoto, director in charge of the No. 2 Vehicle Development Center. Okamoto explains that platforms will be modified and improved with each new model launch. Unlike Honda, however, Toyota prefers to stagger launches of regional variations of its world base models. As a result, the U.S. Camry has evolved to the point it is no longer the same car as the Japanese Camry, each having completely distinct platforms.
Okamoto claims that with each new model, the automaker expects to carry over 70% to 80% of componentry; the remaining 20% to 30% will constitute modifications and upgrades. In this way, he believes Toyota can constantly keep its products and technology "current" while offering distinctiveness between lines.
In the future, Toyota's front-drive lineup will include the Funcargo/Funcoup, replacement for the Starlet; Corolla/Camry; and wide Camry/Windom including the Avalon. Rear- and four-wheel-drive models are more problematic, although the automaker reportedly is trying to consolidate models like the Estima, a mid-ship, rear-drive minivan, with the front-engine, rear-drive Town Ace, Lite Ace, Hiace Regius and Granvia vans. If possible, though more problematic, they would like to include the Hilux Surf sport/utility (sold as the 4-Runner outside Japan).
The task is made more difficult because the five minivans have monocoque bodies while the Hilux Surf employs a subframe structure. Then there will be models like the new Harrier, a sport/utility built on the front-drive "wide" Camry platform (North American model), but having both a front-wheel and four-wheel drivetrain.
TARGETING 'HARD' POINTS...
Another key to keeping development costs under control, specifically to restrain investment in new tooling and facilities, is matching "hard" points on the body of an outgoing or existing model with the hard points of a new model. Hard points include A, B and C pillars, side members, suspension pickup points, engine compartment and the height of the cowl. Says one official: "If we can keep the same geometry, it's possible for us to launch a new model without having to tear up the body shop."
Honda is regarded as the industry leader in this area, though others are not far behind. The automaker's launch of six new recreational models from late 1994, along with a remodeled Civic, Accord, Prelude and Legend, was accomplished with minimal investment in facilities, apart from extremely short lead times. From fiscal 1991 through 1997 (ending this March), Honda's yearly capital spending budget in Japan was less than half what it was between fiscal 1985 and 1990.
Other companies have made similar cuts, but spending patterns are less clear because of the opening of four large assembly plants (two by Toyota and one each by Nissan and Mazda) from 1988 to 1992. Still, in the five years through fiscal 1996, Toyota, Nis-san, Mitsubishi and Mazda spent an average of $3.9 billion on facilities, compared to $6.3 billion in the previous five years.
REDUCING PROTOTYPES...
All companies are working to reduce prototypes. This is being accomplished through simultaneous engineering including expanded use of three-dimensional computer-aided design (3D CAD), digital mockups of assembly operations, and computer simulations of crashes and other structural tests.
The combined effect of these measures has been a significant reduction, in some cases elimination, of first-generation prototypes. Mazda, for instance, is estimated to have built just 250 prototypes for the new Capella wagon and sedan, down 20% from 1995 levels. Mitsubishi only needs 150 prototypes for a standard model like the Galant sedan. If the company develops several variations (two-door, four-door, station wagon) for two or three major markets (North America, Europe and Japan), it can do so with only 300 prototypes.
Hiromi Araki, chief operating officer at Toyota Caelum Inc., a Toyota software unit, predicts that prototype numbers will be cut by another third in the coming two to three years. "By using CAD data," he explains, "we can eliminate the first set of prototypes, those for production preparation, thus lowering costs."
And Japanese carmakers are investing millions to pursue this end. Within the past three years, they have purchased 17 new supercomputers, including 10 from Cray Research Inc., at an estimated cost of $120 million to $125 million. In the process, companies have raised computing capacity sevenfold to 147 gigaflops, from fewer than 20 gigaflops in early 1995. (A gigaflops is equal to 1 billion floating-point operations per second [flops], 1,000 times more than one megaflop. Floating-point operations are able to handle large numbers quickly, thus are particularly useful for graphics.)
More recently, Nissan, Mitsubishi and Mazda have revealed plans to spend in excess of $120 million for computer-aided design, engineering and testing software and systems. Nissan and Mazda have joined with Ford Motor Co. to purchase software from Structural Dynamics Research Corp.; Mitsubishi is switching to "CATIA-CADAM," the same system employed by Honda, Isuzu, Fuji and Suzuki.
Claus Regge, a Tokyo-based technology consultant, notes that the Japanese already are the world's low-cost producers. "By speeding the process from design approval to mass production, this could add to their advantage."
As well as to the concerns of their foreign competitors.
About the Author
You May Also Like