Porsche Points the Way--911's all-new chassis gets light on high-strength steel
The steel industry's rapid mobilization to maintain steel's competitiveness in the automotive sector is one of the more successful concerted supplier efforts in memory. The Ultra Light Steel Auto Body (ULSAB) consortium, made up of 35 steel producers representing 18 nations, recently put the finishing touches on its prototype body-in-white that weighs, on average, 25% less than standard-steel bodies
June 1, 1998
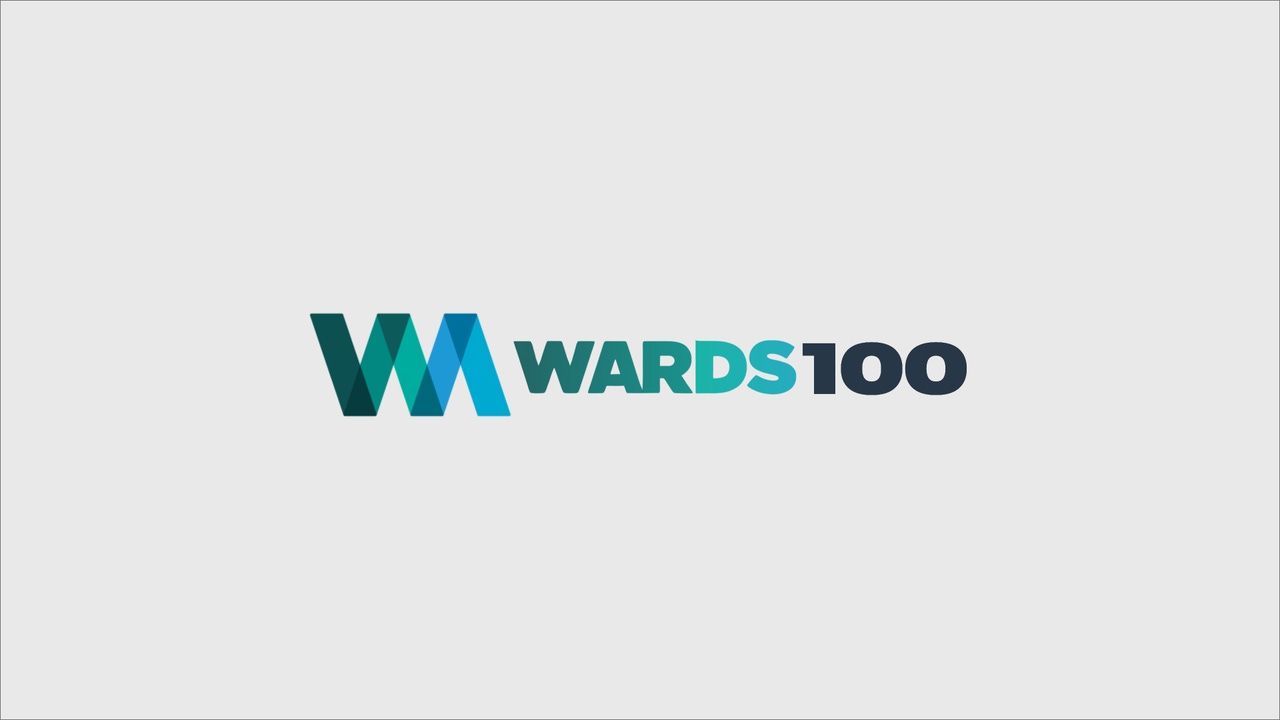
The steel industry's rapid mobilization to maintain steel's competitiveness in the automotive sector is one of the more successful concerted supplier efforts in memory. The Ultra Light Steel Auto Body (ULSAB) consortium, made up of 35 steel producers representing 18 nations, recently put the finishing touches on its prototype body-in-white that weighs, on average, 25% less than standard-steel bodies - yet in many ways is stronger.
One of the key players in the ULSAB project is Porsche Engineering Services - an outfit allied, obviously, with German automaker Porsche AG. The interesting tie-in here is that while the ULSAB members are steel producers pitching ULSAB's advantages to automakers who may be considering employing alternative materials for future vehicle designs, Michigan-based Porsche Engineering has a rather more direct line to an automaker: the Porsche Mother Ship in Stuttgart.
"What the heck," you can hear the Porsche engineers cajoling in a trans-Atlantic conversation with their brethren in Michigan, " $22 million went into this ULSAB thing. Show us what you've done that we can use."
Out comes Porsche's all-new 911 Carrera (see p.53), its chassis incorporating many ULSAB assets: high-strength steel, tailored blanks, laser welding and optimized gauging for the best strength at the lowest possible weight. None of these are new ideas, but using them in concert produces a chassis that's pretty stiff and pretty light.
For the new 911, that means an increase in torsional stiffness by 45%, a bending mode improvement of 50% over the outgoing model, which didn't sport a rubber-band chassis itself. The ultimate proof of optimized high-strength steel design, though, is in the fact that those demonstrable torsion and bending gains are delivered with a concurrent drop in curb weight; the old manual-transmission Carrera Coupe weighed 3,064 lbs. (1,390 kg), the stiffer, stronger '99 equivalent weighs 2,910 lbs. (1,320 kg).
We can't confirm this, but the '99 911 chassis may utilize the most high-strength steel (see chart) of any current production vehicle. The car also employs a small but significant amount of boron steel, which is high-tech stuff even for Porsche and the ULSAB boffins.
Porsche says the boron steel - employed in the door side-impact beams and front and rear chassis crossmembers - is uncommonly strong, but requires delicate handling because it's nigh on impossible to bend once it's cooled. The boron steel is formed in a press-hardening process that inserts the form into the die while it's still warm, then allowed to cool in the mold, conforming to the proper shape.
One industry source says it isn't surprising Porsche decided to use so much high-strength steel in its new 911, because Porsche expects high levels of chassis rigidity and refinement, adding, "The boron thing is pretty exotic; it's good for low-volume builds and perfect for someone like Porsche."
But if you're thinking so much high-strength steel usage is acceptable for a vehicle like the 911 because it's not only a low-volume but high-cost, the ULSAB wants to dispel the perception that high-strength steel construction is more expensive and time-intensive.
"The ULSAB structure is no pie-in-the-sky design," says the American Iron and Steel Institute's Robert J. Darnall at a recent unveiling of the finished ULSAB body-in-white. "We believe an auto company could incorporate these ideas into nearly anything on the drawing board today and just go ahead and build it."
Porsche's already on the way.
About the Author
You May Also Like