Amcast Automotive leads in critical component conversion to aluminumAmcast Automotive leads in critical component conversion to aluminum
With a long history in refining several casting processes and proven advances in alloy development, Amcast Automotive has become one of the pre-eminent suppliers specializing in the conversion of high-integrity performance-critical automotive components to cast aluminum.By converting high-volume applications formerly made of heavier metals to aluminum, Amcast Automotive can produce aluminum components
September 1, 1996
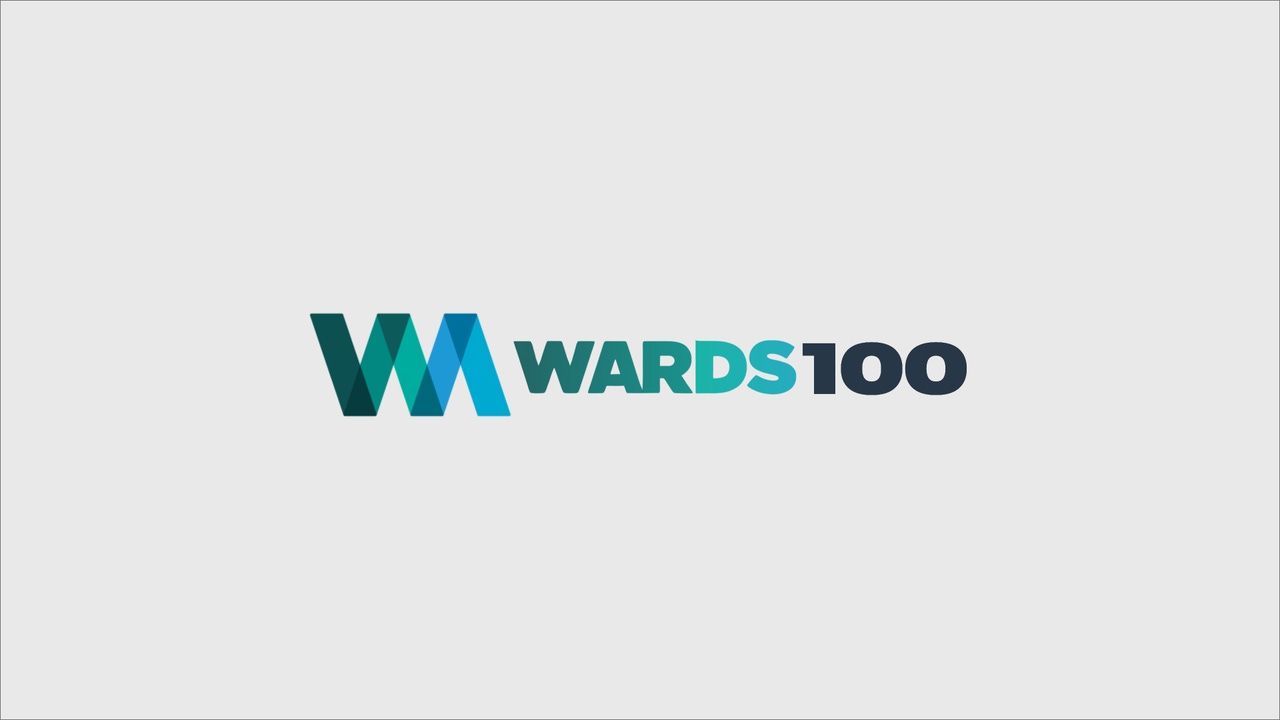
With a long history in refining several casting processes and proven advances in alloy development, Amcast Automotive has become one of the pre-eminent suppliers specializing in the conversion of high-integrity performance-critical automotive components to cast aluminum.
By converting high-volume applications formerly made of heavier metals to aluminum, Amcast Automotive can produce aluminum components that equal or exceed the strength of their cast iron or stamped steel counterparts at greatly reduced weight.
Amcast processes provide high added value in converting these parts: cast aluminum components are light-weight, yet offer superior integrity, closer tolerances and higher strength. Since most performance-critical components are cast into permanent molds, they require less machining and finishing, maintain a good surface appearance, and are thus cost-effective from the customer's point of view.
Front Control Arm
Normally a stamped steel fabrication weighing about 3 kg, the design is stiffness driven for vehicle ride and handling performance. In converting this component to aluminum, lightweight alloys must be selected to withstand the load demands associated with cornering, braking, acceleration and rough road conditions.
In one case, Amcast Automotive designed and produced a high-strength aluminum alloy front control arm casting with a finished weight of 2.2 kg. This design has 12mm walls in high-stress areas and a 5 mm web section for stiffness against twisting forces.
Lower Trailing Arm
Strength, stiffness and crashworthiness are the design criteria for this performance-critical suspension component. Normally a stamped steel part weighing about 20 kg, Amcast has proven that a weight reduction of 40 percent is possible.
Front and Rear Knuckles
Traditionally cast in ferritic ductile iron, knuckles are produced either by annealing or by controlling the manganese content in the casting process. Typical weight is 3 to 4 kg. Redesigned as aluminum castings, a weight reduction of 40 percent has been achieved with excellent performance and durability characteristics.
Brake Calipers
Another safety-related, critical-performance component is the brake caliper. Brake calipers need to maintain a stiff bridge throughout the brake operating temperature range. Traditionally made of ductile iron and weighing about 4 kg, Amcast Automotive has produced gravity permanent mold aluminum brake caliper castings weighing half as much as their cast iron counterparts.
Differential Carriers
A typical light vehicle differential carrier is cast in ductile iron and weighs 15 to 20 kg. Rear-wheel-drive sport and luxury cars, as well as 4WD trucks, are prime candidates for a differential carrier conversion to aluminum, providing a better weight distribution between the front and rear axles.
Amcast cast aluminum differential housing walls are thin, but ribbed for rigidity to ensure there is no deflection of the interior gears. The casting design results in a heavy pinion housing and a strong and rigid bowl face connected by a thin-walled but ribbed bowl. In one case, the finished, high-strength casting weighed 45 percent less than the cast iron design.
You May Also Like