Castaing's holy grail: Convergence '96 seeks the seamless electromechanical vehicleCastaing's holy grail: Convergence '96 seeks the seamless electromechanical vehicle
Induction restriction is reduced through the use of a larger throttle body, larger intake take valves and a larger throat area. These refinements allow for increased airflow into the intake ports and combustion chambers. Composite manifold runner surfaces also reduce air friction and allow more air to flow through the system.At the exhaust end, valve size, exhaust port shape, exhaust pipe size. manifold
December 1, 1996
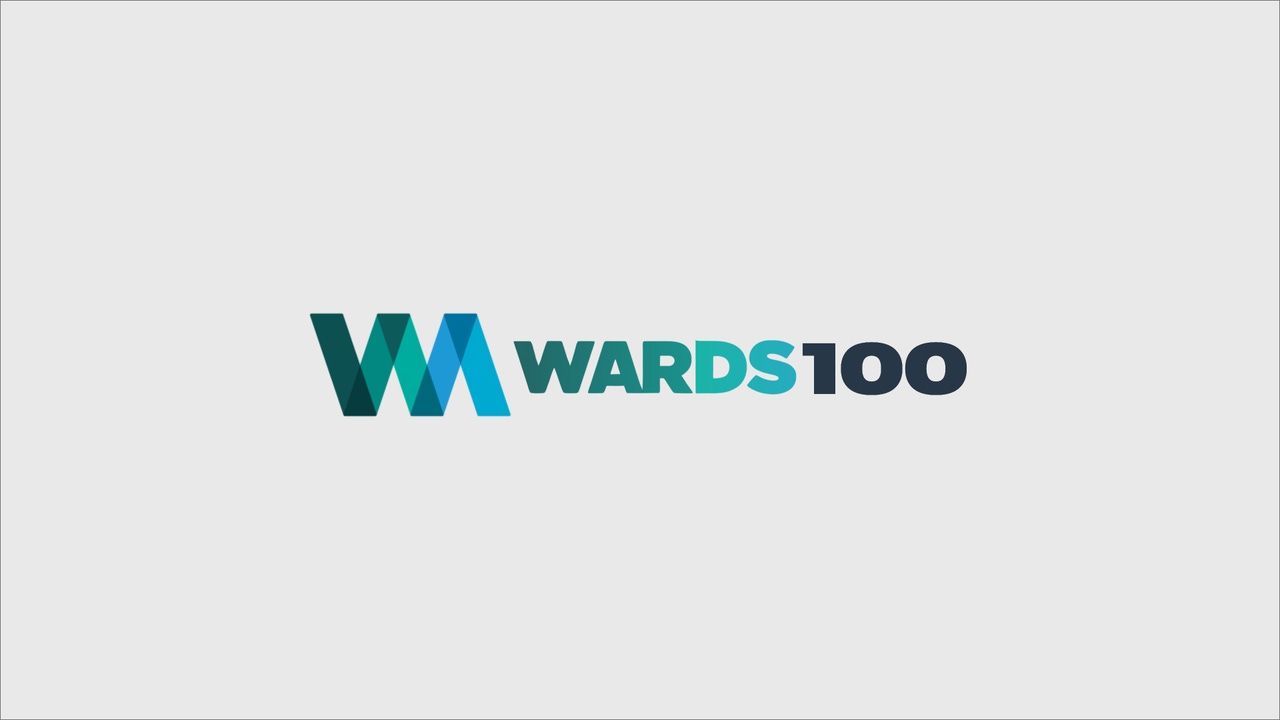
Induction restriction is reduced through the use of a larger throttle body, larger intake take valves and a larger throat area. These refinements allow for increased airflow into the intake ports and combustion chambers. Composite manifold runner surfaces also reduce air friction and allow more air to flow through the system.
At the exhaust end, valve size, exhaust port shape, exhaust pipe size. manifold and catalytic converter entrances are all optimized for maximum flow out of the engine, decreasing back pressure and increasing exhaust flow.
Chrysler engineers also tackle strength and rigidity issues with the new V-6s. The aluminum engine blocks are heat-treated, making them stronger than many cast iron blocks. Combining the proven wear-resistance and durability of iron with the lightweight properties of aluminum, cast-iron cylinder sleeves are cast directly into the aluminum block. Cylinder bores are then finished to a tolerance of 0.3 microns.
Forged steel crankshafts replace the iron ones found in the current engine lineup. also significantly improving stiffness.
Moreover, a 15% reduction in piston mass and a reduction in the tolerances of all rotating components greatly suppresses torsional movement of the block. with reductions ranging from 10% in the 3.5L to 27% in the 2.7L.
Component wear is diminished with the use of a "coil-on-plug" sparkplug design - the placement of ignition coils directly on top of platinum-tipped spark plugs - a setup that eliminates the need for secondary ignition cables, which Chrysler fingers as a component particularly prone to wear. Consequently, the new engines should run 100,000 miles (162,000 km) between scheduled tune ups.
All three engine cranks enjoy 6-bolt, cross-bolted main bearing caps. A die-cast aluminum structural beam then connects the bearing caps and doubles as a windage tray, separating the oil pan from the crankshaft to prevent air-frothing of the oil. Chrysler determines the structural beam increases block rigidity by 28%.
Other stiffness refinements include the addition of reinforcement ribs on the transmission case and an aluminum transmission collar that bolts the transmission to the oil pan, integrating the oil pan into the powertrain structure. All the stiffness work delivers lower noise/vibration/harshness (NVH) levels.
To further battle NVH, Chrysler designed the valve covers to better isolate valvetrain noise and optimized the main bearing size to reduce crank rotational noise. The 2.7L features a uniquely designed, "low-rumble" intake manifold tuned to produce a distinctive sound while maximizing intake and combustion efficiency. Airflow paths of equal length (from the throttle body to each cylinder) also aid in NVH alleviation.
On average, the engines deliver up to 24% more horsepower than the V-6s they replace, with 10% better fuel economy. They'll also produce fewer emissions and will meet Tier 2 federal emissions and California's Transitional Low Emission Vehicle (TLEV) standards in 1998. They'll also be able to meet California's Low Emissions Vehicle (LEV) standards for 2000.
Because a large portion of any vehicle's emissions are produced during cold starts, Chrysler engineers responded by reducing the size of the exhaust manifold to accelerate catalyst warm-up times. The catalytic converter also is a close-coupled design to reduce light-off time.
Higher compression ratios also allow the engines to more efficiently burn fuel and improve fuel economy and performance, and anodized piston heads lessen the amount of hydrocarbons clinging inside the cylinder, allowing for more complete combustion. Combustion rates also are improved through the incorporation of electronic exhaust gas recirculation (EEGR). EEGR reduces the emissions of hydrocarbons (HC) and oxides of nitrogen (NOx).
Because Chrysler eschews the need for premium-grade gasolines in an of the new V-6s, performance is optimized through the installation of knock sensors.
The result: a 30% reduction in overall engine hydrocarbon emissions, Chrysler boasts.
Chrysler will tool up the two engine plants with combined annual capacity for 640,000 of the new V-6s. Production is slated to begin in August 1997, but the company won't say how long it will take to hit full capacity levels.
You May Also Like