High-quality casting processes for aluminumHigh-quality casting processes for aluminum
To meet the increasing demands of automotive designers, Amcast Automotive has invested heavily in developing new technology to produce aluminum castings. This investment has led to continued refinement of its casting processes through advanced engineering and process development, resulting in unequaled expertise in the production of high-integrity products for the automotive industry. Automakers are
September 1, 1996
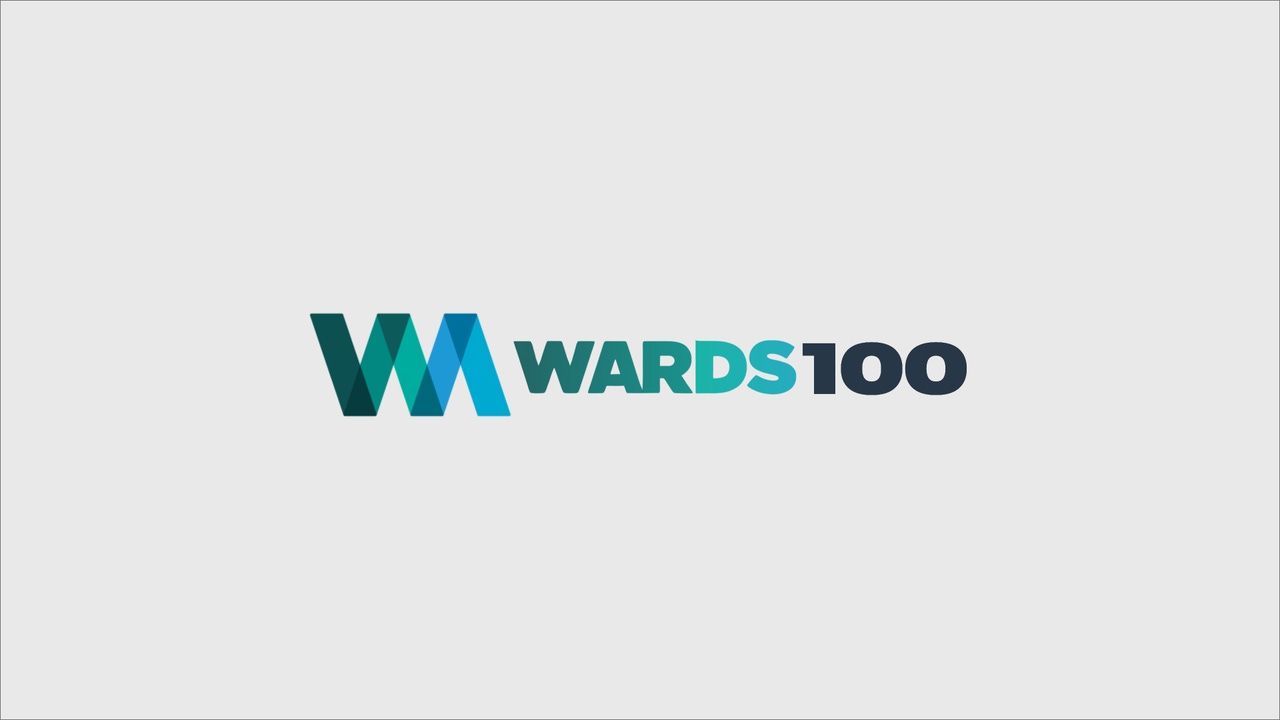
To meet the increasing demands of automotive designers, Amcast Automotive has invested heavily in developing new technology to produce aluminum castings. This investment has led to continued refinement of its casting processes through advanced engineering and process development, resulting in unequaled expertise in the production of high-integrity products for the automotive industry. Automakers are increasingly adopting Amcast aluminum components as a viable alternative to heavier metals in meeting CAFE requirements through reduction of vehicle weight.
Recognizing this trend, Amcast has consistently focused on aluminum conversion for automotive components in which structural integrity and reliability are critical. With a total program management and leading-edge casting technology approach, Amcast has successfully designed and produced a wide range of high-integrity performance-critical components. These include cast aluminum wheels, brake system components like master cylinder housings, caliper castings and antilock brake system (ABS) modulator valve housings and power steering valve housings.
Suspension components include spindles, upper and lower control arms and knuckles. Powertrain and chassis component experience includes differential gear housings and cross members. Climate control system parts range from scrolls to tubular manifolds.
While Amcast's processes differ widely in the types and sizes of parts produced, all share the common characteristics of high production capability, competitive costs, and high product integrity.
Gravity Permanent Mold Casting
Amcast produced the first-ever high production cast aluminum suspension component in 1989, a GPM-cast knuckle still in production on a mid-size automobile. Before this, Amcast produced the first US high production aluminum brake caliper with the GPM process.
Using computer-controlled equipment throughout, Amcast rotary casting machines take the mold to the metal for high-volume efficiency. Up to 14 die stations are mounted in a rotating platform which delivers each mold to a dispenser that fills each with the precise amount of aluminum alloy.
As the platform rotates, mechanized equipment tips the mold precisely, optimizing metal flow and minimizing turbulence. Temperature controls monitor cooling and control solidification. Combined, these features ensure porosity-free castings with high mechanical strength. Robots extract cast parts for cooling and automated trimming.
Heat-treated castings are transferred to CNC machining cells and assembly stations when "bolt-on" finished assemblies are desired.
Light Cast System
Amcast's Light Cast System (LCS), a low-pressure permanent mold casting process, is used when performance is critical and part geometry is complicated, as in lightweight cast aluminum wheels or complex suspension and driveline components.
Compared to other casting processes, LCS is particularly versatile and adept at handling large structural parts up to 1 m, with weights up to 20 kg.
In specially designed LCS casting machines, in which the holding furnace is located below the tooling, molten aluminum is forced up through the center of the mold via a double-filtered fill tube. The center-fill method cuts waste in the feeding system. Center-fill molds also allow more design flexibility, since the technology facilitates directional solidification. The capability to provide high integrity and to accommodate thick and thin sections, slides, and cored holes allows substantial design freedom.
Programmable logic control and special rapid cooling methods provide high process repeatability and high mechanical strength, thus ensuring the overall integrity of the product.
Squeeze Casting
Amcast's proprietary Hi-CAST[TM] squeeze casting process reaches new levels of integrity and strength. The Hi-CAST[TM] process uses a fully integrated production cell and an innovative double-piston intensification or squeeze system. Sophisticated central processing units control the process, coordinate machine functions, and control material flow and the casting solidification sequence.
This process delivers premium castings with the higher mechanical properties needed for many performance-critical applications, like front suspension knuckles and compressor scrolls.
Porosity free, near-net-shape parts often translate into raw material and machining cost savings. Consistency yields greater design freedom and excellent internal integrity across thick and thin sections.
You May Also Like