Flexibility Key to Managing Global Supply Chains
The trend toward globalization has become risky due to factors including unsettled international relations, ethnocentrism, trade disputes, global counterfeiting, the COVID-19 pandemic and travel restrictions, supply-chain consultant Rosemary Coates says.
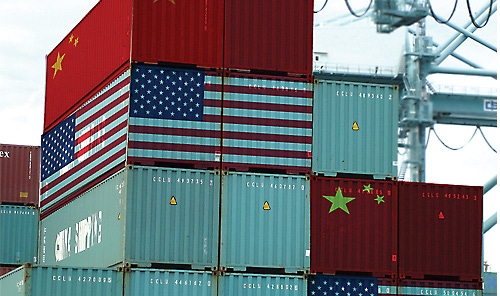
Global supply chains face risks ranging from trade wars to counterfeiting to the COVID-19 pandemic, and foresight and flexibility are the key for manufacturers trying to operate efficiently and without interruption, a trade expert says.
“You should have a Plan A, a Plan B, a Plan C and sometimes a Plan D,” Rosemary Coates (below, left), executive director of the Reshoring Institute, says Tuesday during a Festival of Automotive webinar. The nonprofit institute provides consulting, research and other services to businesses seeking to bring cost-effective manufacturing back to the U.S.
U.S. jobs fled during the 1990s and 2000s to countries with low-cost production environments, particularly China, which strengthened its hand by joining the World Trade Organization in 2001, says Coates, a supply-chain consultant for 25 years.
But that trend toward globalization has become risky in recent years due to factors including unsettled international relations, ethnocentrism, trade disputes, global counterfeiting, the pandemic, travel restrictions and the trend toward lean methodologies, which aim to reduce supply-chain inventories, she says. Globalization is countered by actions such as U.S. tariffs on aluminum and steel imports from several countries and tariffs on most Chinese imports.
Coates says regardless of who wins the White House in November, trade wars likely will continue, although she allows for the possibility of reduced tariffs.
For U.S. manufacturers seeking to bring their operations back from China to America, the process isn’t simple, Coates says. Many workers there have employment contracts that would have to be fulfilled if their U.S. employer pulls out; obtaining permits to leave can be time-consuming; wait times can be considerable; tools, dies and molds likely won’t be able to be taken out of China; and intellectual-property issues would have to be resolved, she says.
Rosemary Coates
Strategies for mitigating risk include local-for-local reshoring, or manufacturing within the country where the product is to be sold; China Plus 1, or manufacturing both for the Chinese market and one other country, such as Mexico or Vietnam; rigorous supply-chain oversight; brand- and IP-protection efforts; and re-thinking lean methodologies, Coates says.
Manufacturers also should be aware of the risks of single sourcing and may want to consider a backup source or even operating in a second country to guarantee the integrity of the supply chain. “You can’t build a car with just three wheels,” Coates says.
Besides building flexibility into their global supply chains, manufacturers should practice their responses to different scenarios, making preparations and updating them annually, she says, adding having an alternate strategy is crucial for dealing with COVID-19 disruptions.
Panelists at the Center for Automotive Research’s virtual Management Briefing Seminars held earlier this month said the pace of reshoring to the U.S. has slowed as businesses continue dealing with the fallout from the pandemic.
Chad Moutray, chief economist for the National Association of Manufacturers, said some 750,000 manufacturing jobs have disappeared since February, and he expects recovery won’t take place until 2022.
About the Author
You May Also Like