After 60 Years, a New Way to Prime-Coat Vehicles
Chemical supplier Henkel is introducing new technology to the 60-year-old phosphate pretreatment process.
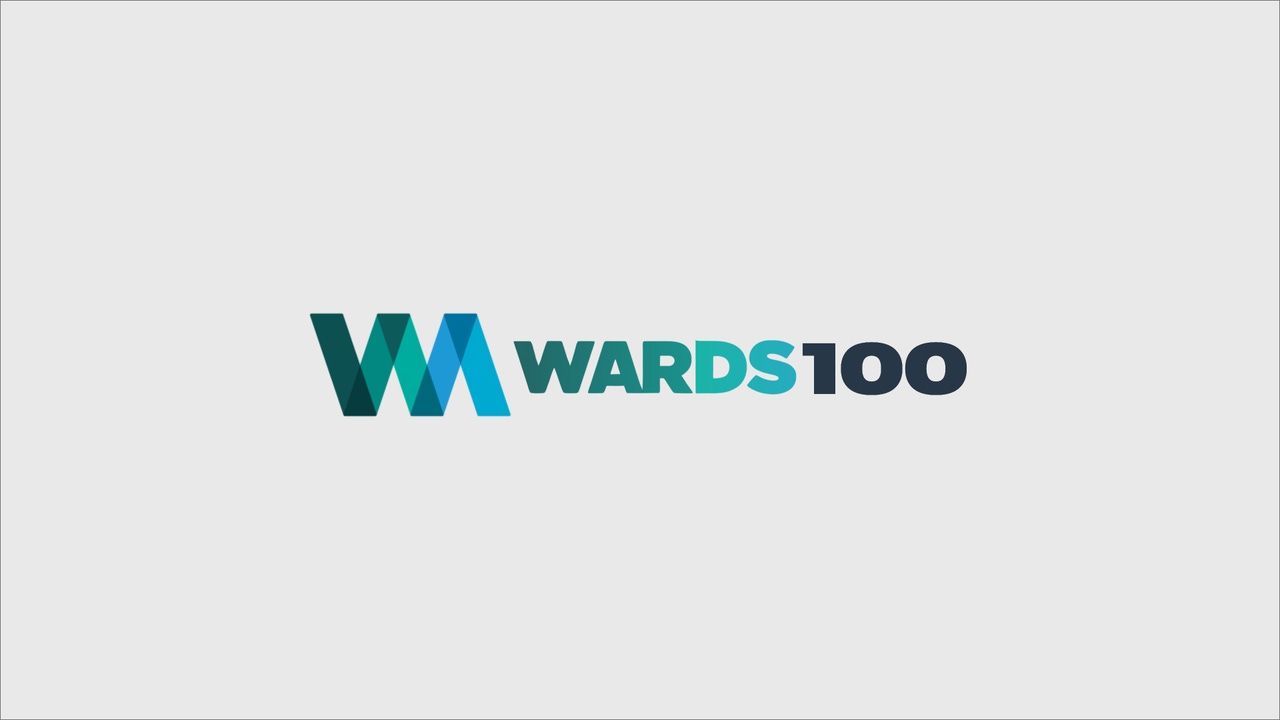
Special Coverage
SAE World Congress

DETROIT – Every household painter knows prepping and priming is one of the toughest parts of the job. Painting vehicles isn’t much different.
Vehicle bodies must go through extensive cleaning and pretreatment stages before they are ready for the paint booth, and that process is expensive, time-consuming and energy intensive.
One of the first metal pretreatment steps is the so-called phosphate dip, where vehicle bodies are immersed in a chemical bath of zinc phosphate that acts as a primer coat for the metal surfaces.
This operation has existed in automotive paint shops for about 60 years and largely has gone unchanged since the 1980s, says Dan Wohletz, vice president-automotive North America for Henkel Corp.
Now Henkel, a major supplier of chemicals to the auto industry – including zinc phosphate – is aiming to obsolete itself with a new non-phosphate pretreatment process.
Henkel has partnered with Ford Motor Co. to implement a new version of its existing Bonderite coating process it is touting at the SAE International World Congress here.
Wohletz says the new coating process cuts costs, streamlines vehicle assembly plant pretreatment operations and reduces the environmental impact from the manufacturing process.
Vehicle body runs through conventional phosphate dip prior to painting.
All told, the new process can save an auto maker $500,000 annually when it is retrofitted in a brownfield facility, even more when installed at a greenfield site, Wohletz says.
Ford already has produced some production pilots using the technology and could put it into regular production as early as the end of this year or in 2008.
The new Bonderite procedure uses an ultra-thin nanoceramic coating in place of zinc phosphate and eliminates several steps of the conventional phosphating process. This shortens the length of the production line, improving throughput and cuts energy costs.
Eliminating phosphate also significantly reduces plant wastewater treatment and costs associated with disposing of the phosphate sludge that builds up in conventional dip tanks, Wohletz says.
Read more about:
2007About the Author
You May Also Like