French Researchers Driven to Cut Vehicle Weight
One expert says consumers must be sold on the idea that the higher manufacturing costs of key lightweighting materials are offset by long-term fuel savings.
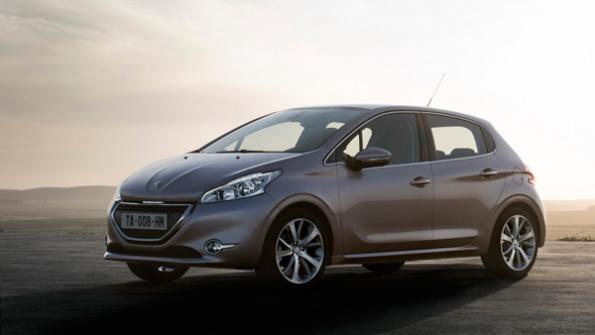
PARIS – Composite materials and mass production continue tentatively dancing around each other, but by the end of the decade French auto makers expect to see structural composites in their mass-market cars.
Renault and PSA Peugeot Citroen are working together on FASTLITE, a research-and-development project aiming to take 440 lbs. (200 kg) out of their vehicles by 2018-2019.
The project, subsidized by the French government, involves a dozen suppliers, research labs and universities. The auto makers expect it to result in new modeling tools as well as new materials.
In a joint presentation at the annual JEC composite show here, PSA representatives say composites are competitive as nonstructural panels.
But composites are not ready for structural duty in high volume, they say, because materials generally are too costly; current manufacturing technology allows only drop-in parts, not complete new architectures; design and simulation tools are rare; and superior performance is not enough to overcome low confidence.
“Composites need to respond to all requirements,” says Gerard Liraut, head of Renault’s polymers and fluids department. “Risk makes managers nervous.”
FASTLITE members include Plastic Omnium, which displayed a prototype vehicle at last year’s Frankfurt auto show.
The prototype demonstrated that parts like a B-pillar could be made of composite material, with a steel plate attached top and bottom so that it could be a “drop-in” part in an auto maker’s body shop, handled by robots and welded to the rest of the body in white.
Carbon fiber is too expensive for mass production, says Louis David, the senior materials expert at PSA. Even when considering the fuel that would be saved by using carbon fiber, the lifetime cost of the car would be higher.
On the other hand, he says the weight reduction resulting from use of sheet-molding compound is more economical in the long run because the money consumers save by using less fuel exceeds the extra manufacturing cost
To use that argument for SMC requires that consumers have a total cost of ownership mindset. And while commercial-fleet managers have that outlook, the average car buyer does not.
David notes that over the years there have been many lightweight prototypes and concept cars, but only a handful of niche vehicles have made it to production, including the Corvette Z06, Audi A2 and A8, Jaguar XJ and Honda NS-X.
He cites a presentation from the Massachusetts Institute of Technology comparing extra costs of different materials with the possible weight savings. High-strength steel adds €1 to €2 ($1.33 to $1.66) per 2.2 lbs. (1 kg) and saves 5% to 20% of mass, while carbon fiber adds €10 to €16 ($13.30 to $21.25) in manufacturing cost to save 40% to 60% in mass.
In other words, David says, lightweighting always costs more to manufacture. However, when subtracting lifetime fuel savings from the additional production costs, high-strength steel, SMC and glass-fiber composites all show savings in total cost of ownership.
The mass in most of today’s cars is 60% steel, 20% plastic and 10% aluminum, mostly in the powertrain.
The average Renault and PSA car emits about 130 g/km of carbon dioxide. Although both auto makers offer individual models below 100 g/km, they need to reduce the mass of their vehicles to reach Europe’s 2020 goal of 95 g/km (and PSA’s own goal of 90 g/km).
“In 2020, 85% of cars will still use internal-combustion powertrains,” David says.
The potential improvement in powertrains is about 10%, or 13 g/km, and aerodynamics and rolling road resistance might add another 4 g/km, which could reduce the fleet average to about 115 g/km. To reach 95 g/km, auto makers would have to take out 440 lbs. (200 kg) of mass.
“We need to reduce vehicle mass for each new car,” Dasvid says. “Weight saving is an environmental imperative. We need to save 80 kg to 100 kg (176 lbs. to 220 lbs.) immediately and 200 kg (440 lbs.) and more in the next 10 years.”
The target is 440 lbs. (200 kg) by 2018 and 220 lbs. (100 kg) by 2015. David notes the Peugeot 208 just now coming to market is 220 lbs. (110 kg) lighter than the 207 it replaces.
The trend toward 2020 is to use all the potential of steel technology, with high- and very-high- strength steels that can save 110 lbs. to 154 lbs. (50 kg to 70 kg) at a cost of $1.33/2.2 lbs. (€1/kg), Renault’s Liraut says.
Cars will use more aluminum, especially on the body in white, as the powertrain already is in aluminum and can yield potential weight savings of 330 lbs. (150 kg). As polymers and composites become an alternative to aluminum, and cars start using composites for structural parts, potential weight savings will reach 440 lbs. (200 kg).
A robust supply chain is critical to successfully bringing structural composites to mass production, Lairut says. It needs to be solid and reliable from the supply of material to the Tier 1 or the OEM that conceives the part.
“For cost and technology reasons, we believe that the 2020 car will be designed with a mix of steels, aluminums and plastics/composites,” he says. “Volume and cost will be secure for all new materials, and if we can preserve steel, we will do it, but composites are the most promising way.”
The FASTLITE program is part of France’s €35 billion ($46.5 billion) investment over the coming decade to ensure its industrial future. “FASTLITE is the French solution,” David says. “It is a strong program for weight reduction. The objective of the government is employment.”
For auto makers, the objective is to develop materials, modeling software and manufacturing- and-joining technologies.
“We are not sure that the materials needed are existing today,” David notes. “We need modeling tools, automation, numeric tools; and our teams need to learn how to design composite parts.”
About the Author
You May Also Like