Ford Feeds Suppliers Blue Collars for LaunchFord Feeds Suppliers Blue Collars for Launch
TRAVERSE CITY, MI Ford Motor Co.'s hourly workers are being sent to suppliers during launch ramp-ups in order to smooth out rough edges that potentially could lead to costly delays. Ford has whittled its ramp-ups down to a 30-45 day period, Jim Tetreault, director-car manufacturing operations, says at the Management Briefing Seminars here. The month-and-a-half window represents a dramatic cut from
August 2, 2005
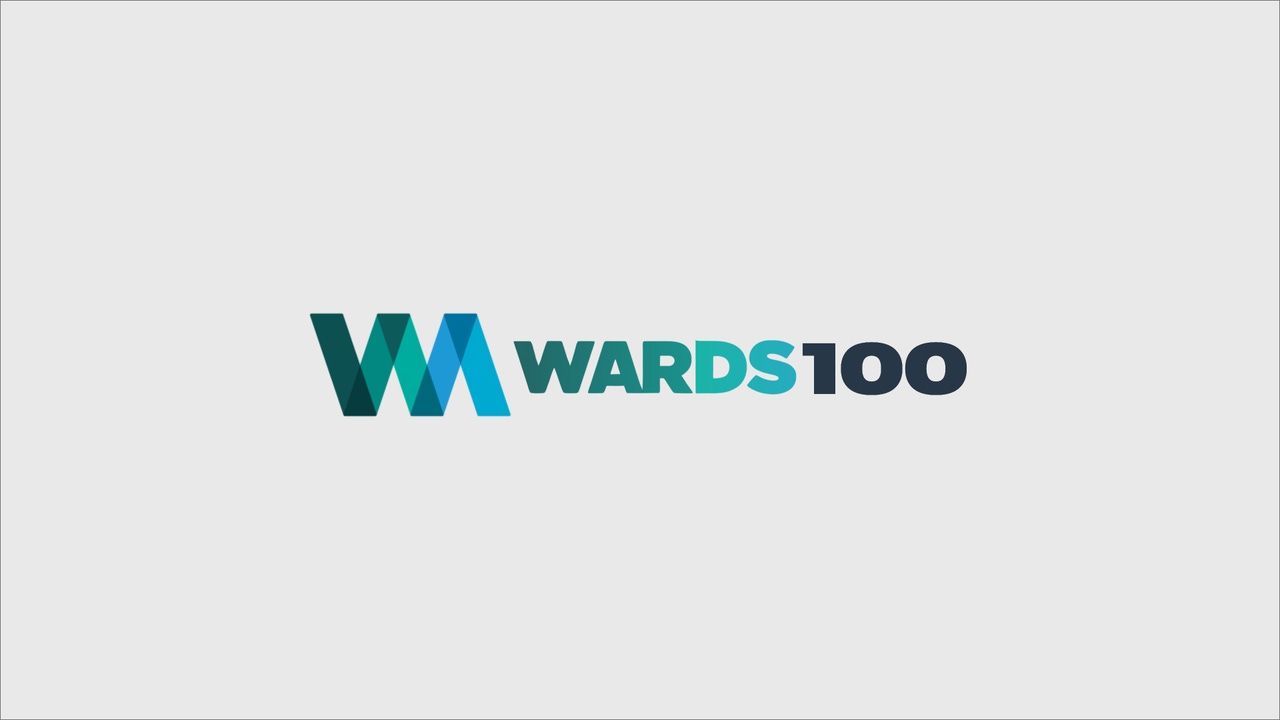
TRAVERSE CITY, MI – Ford Motor Co.'s hourly workers are being sent to suppliers during launch ramp-ups in order to smooth out rough edges that potentially could lead to costly delays.
Ford has whittled its ramp-ups down to a 30-45 day period, Jim Tetreault, director-car manufacturing operations, says at the Management Briefing Seminars here.
The month-and-a-half window represents a dramatic cut from days gone by, when launch ramp-ups could eat up as much as a year. Tetreault credits hourly labor with facilitating the cut.
He says blue-collar workers started getting more heavily involved during the '97 F-Series launch and have become more intimate with the gritty details of ergonomics, production logistics and parts sorting since then.
Jim Tetreault says hourly labor heading to suppliers to help launches.
The auto maker's most recent push includes sending United Auto Workers union employees into the virtual build studios, where Ford designs a car digitally with the help of line labor in order to ensure manufacturing compliance before prototyping in hard clay.
Now, Ford is lending some of those workers to suppliers as far out as a year before launch in order to speed along the process throughout the supply line and ensure quality at Job One, Tetreault tells Ward's.
The auto maker calls the cadres of hourly launchers “supply-based launch teams.” “We're doing this where there is pull,” Tetreault says, noting a supplier needs to ask for help in order to get it.
Having supplier parks installed at some manufacturing plants, including Chicago Assembly and Hermosillo, Mexico, which is being retooled for sedan production this fall, has helped foster collaboration between Ford and its parts makers.
“A supplier park certainly makes it logistically much easier,” Tetreault says. In the case of Hermosillo, about 20 suppliers have located around the facility in order to better supply in a lean manner, including bankrupt Collins & Aikman Corp., whose cash shortage could present problems down the road.
The worker-sharing pact with the UAW and suppliers follows a trend of integrating more and more hourly workers, especially skilled tradesmen, into product development for the sake of improving the build-ability of vehicles.
In Ford's case, it needs to encourage similar launch practices at suppliers located both in nearby parks and around the world due to its own rapid progress in trimming ramp-ups.
Tetreault points to the recent Five Hundred sedan and Freestyle cross/utility vehicle launch situation in Chicago, where the auto maker was ready to launch at desired line speed but was waiting on certain components to reach desired volume.
Ford currently is engineering a multitude of launches where lending hourly help to suppliers may be necessary. Launches for '07 models include two new CUVs coming from Oakville, Ont., Canada, and new large SUVs from Wayne, MI. (See related story: Ford Expects 170,000 Fusion Deliveries in 2006)
Read more about:
2005About the Author
You May Also Like