Greening-Up Toyota's Latest Hybrids
Toyota Motor Corp.'s two newest hybrid cars, the Sai and Lexus HS 250h, have turned decidedly green in their use of eco-friendly materials. The auto maker's main interior supplier, Toyota Boshoku Corp., outfitted each model with more than 10 lbs. (22 kg) of components made from plant-based composites mainly kenaf, a fiber indigenous to Southeast Asia, mixed with polypropylene, a widely used thermoplastic.
October 1, 2010
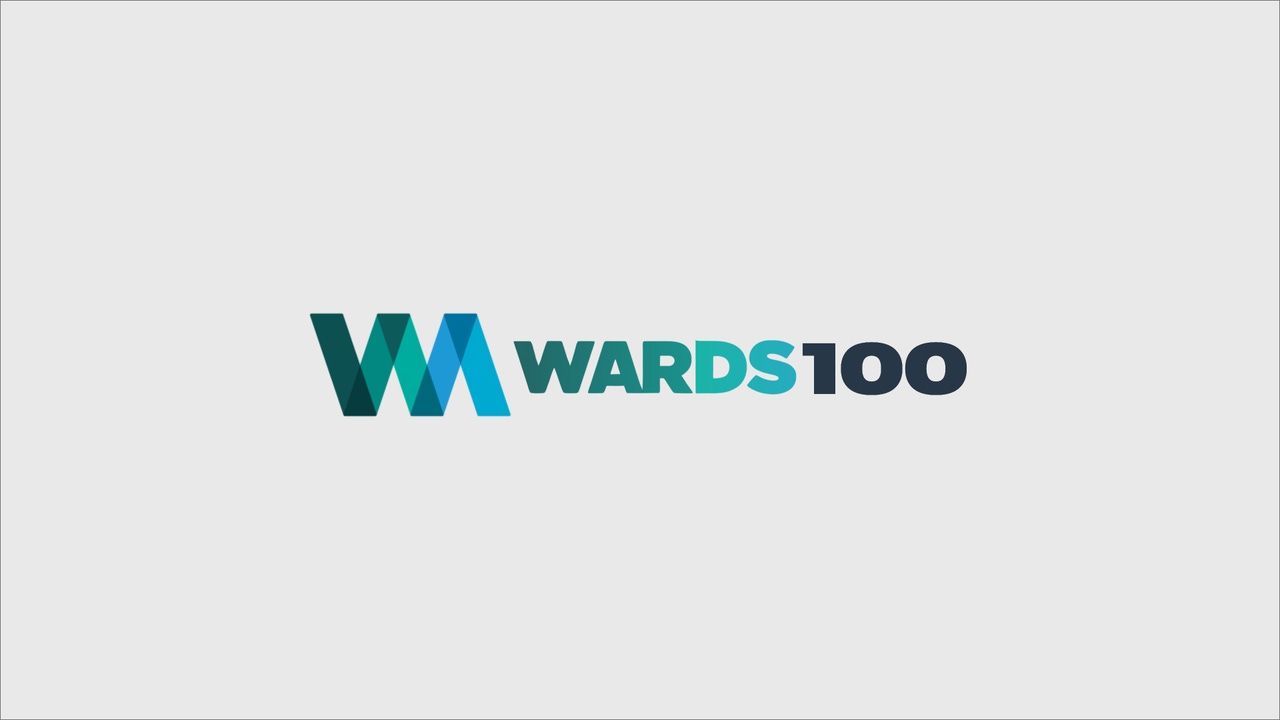
Toyota Motor Corp.'s two newest hybrid cars, the Sai and Lexus HS 250h, have turned decidedly green in their use of eco-friendly materials.
The auto maker's main interior supplier, Toyota Boshoku Corp., outfitted each model with more than 10 lbs. (22 kg) of components made from plant-based composites — mainly kenaf, a fiber indigenous to Southeast Asia, mixed with polypropylene, a widely used thermoplastic.
Special components developed for the HS 250h and Sai include trim for the cowl, door and trunk, pillar garnish, package tray and sun visor and ceiling materials. The supplier estimates 30% of trunk and interior parts are made from plant-based materials.
In addition, Toyota Boshoku now mixes castor oil, a vegetable oil, with polyurethane, a petroleum derivative, to make seat pads. The castor oil penetration stands at 15%.
"Our strategy is to be carbon neutral," says Toyota Boshoku research executive Yasushi Nakagawa. "Where possible, we use plants which do not emit (carbon dioxide) into the atmosphere."
According to Nakagawa, plant-based materials have a second advantage: reducing component mass and weight.
The research executive, who heads Toyota Boshoku's new Sanage Research and Development Center near Toyota City, estimates weight reduction through use of kenaf-based composites — both kenaf and polypropylene and kenaf and polylactic acid composite — to be about 35% compared with conventional plastics.
The supplier introduced its first plant-based component in 2000 with the door trim for the LS 430 luxury sedan, predecessor to the current LS 460.
Since then, Toyota Boshoku has supplied 13 Toyota and Lexus cars and one Suzuki Motor Corp. model, the APV minivan built in Indonesia, with plant-based door trim, seat-back boards and package trays.
The supplier annually consumes 3,000 tons (2,700 t) of kenaf fiber in component production.
Nakagawa admits the material remains relatively expensive. The fiber, after being harvested, must be mixed with polypropylene or polylactic acid fiber to make a mat, then heat-treated and pressed into a board before being molded into the component.
By expanding sales beyond the Toyota group and improving economies of scale, costs will come down close to conventional materials, the executive says.
The supplier has made a financial commitment in kenaf-based materials, having established two technical centers in Indonesia, in Melang and Balipapan, and several plantations in East Java.
In addition to expanding applications for plant-based materials, Toyota Boshoku, Japan's leading car-seat manufacturer, has developed a new lightweight standard seat frame for B-, C- and D-segment cars.
Designated TB-NF110, the frame debuted on the new Prius in spring 2009. It is 3 lbs. (1.4 kg) lighter than previous frames due to expanded use of high-tensile steel.
The frame eventually will be adopted for more than 70% of vehicles in Toyota's lineup — all but luxury sedans, fullsize pickups and super-compacts such as the midget iQ, Nakagawa says.
In January, Toyota Boshoku's Princeton, IN, operation began making the new frame for the '11 Sienna minivan. In the future, it will supply the unit for the North American-built Camry, RAV4 and Highlander.
Toyota Boshoku purchases 980-MPa class high-tensile steel frames and tracks, respectively, from JFE Steel Corp. and Kobe Steel Ltd., which also are shipped to the U.S. for production there.
Nakagawa says the new NF110 series will trim frame weight and bulkiness 10%, warning any additional reduction may require use of carbon-fiber-reinforced plastics or magnesium.
Toyota Boshoku supplies a magnesium frame for the Lexus LS 600h.
"We're developing this capability," the Toyota Boshoku official says. "But these materials are still very expensive. Nevertheless, after engines, transmissions and tire-and-wheel sets, seats are among the heaviest parts in a car."
For emerging markets such as China and India, Nakagawa expects to introduce a new, lightweight frame along the lines of the IQ unit that, through expanded use of molded plastic, is 30% lighter but comparably priced.
The supplier also is making advances in engine parts and is a leading supplier of head covers, intake manifolds and filters.
Last year, it reduced mass of the intake manifold for the 2.5L Subaru Legacy engine 60% by switching from aluminum to nylon-6. For the European Toyota Yaris, it achieved a 40% reduction by integrating the engine head cover with the engine control valve.
In the future, Toyota Boshoku potentially could assemble instrument-panel modules inside Toyota's plants much like Calsonic Kansei Corp. does for Nissan Motor Co. Ltd. "We're confident that we have the capability, but whether that's the direction Toyota wishes to go is another matter," Nakagawa says.
He also believes kenaf and other lightweight materials go hand in hand with the emergence of electric and fuel-cell vehicles that will require smaller, lighter components.
"If seatbacks and frames can be made thinner, we could put the battery below the floor and possibly lower the center of gravity without increasing overall vehicle length," Nakagawa says.
At the 2010 Japan Society of Automotive Engineers exhibition held in May in Yokohama, the supplier displayed a new door weather strip that is 25% lighter. It also showed off a new seat prototype employing a monofilament net material that is 10% lighter than the NF110 unit.
About the Author
You May Also Like